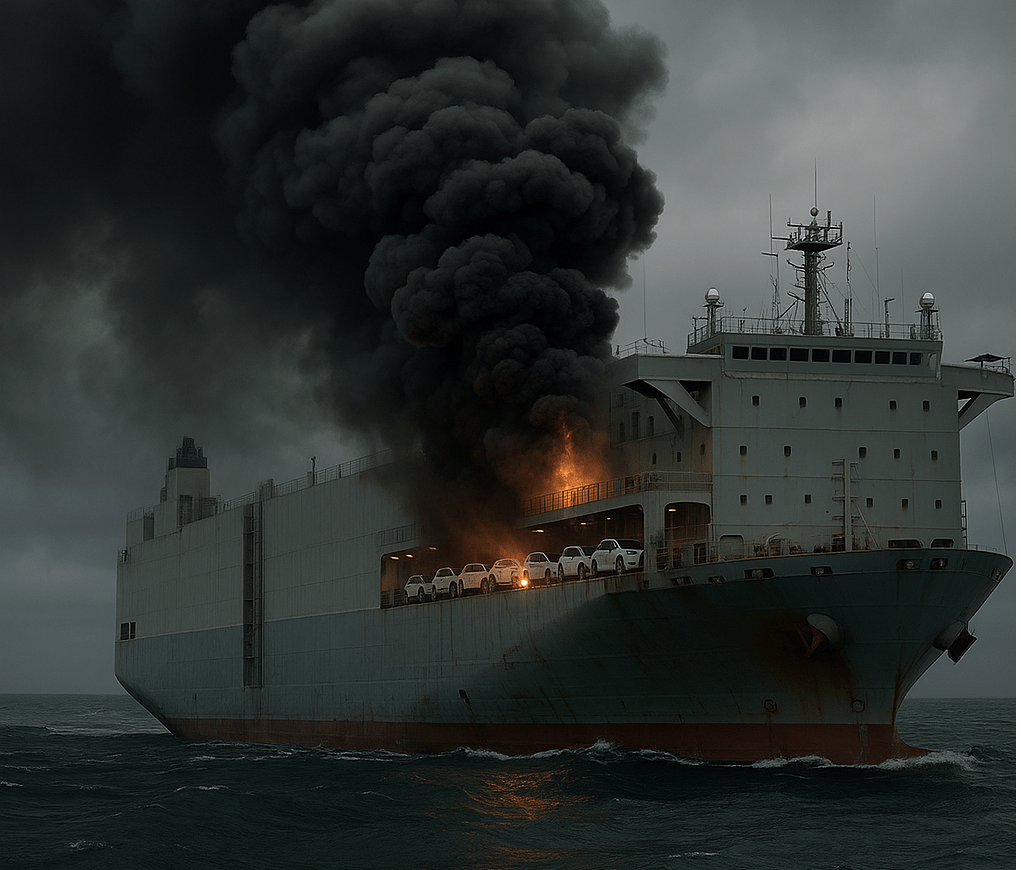
Morning Midas Car-Carrier Fire: What It Means for Safely Shipping Cars & EVs
Early on 3 June 2025, a routine Pacific crossing turned critical when the 19-year-old car carrier Morning Midas reported a fire on one of its vehicle decks. Within hours the 22-person crew abandoned s...