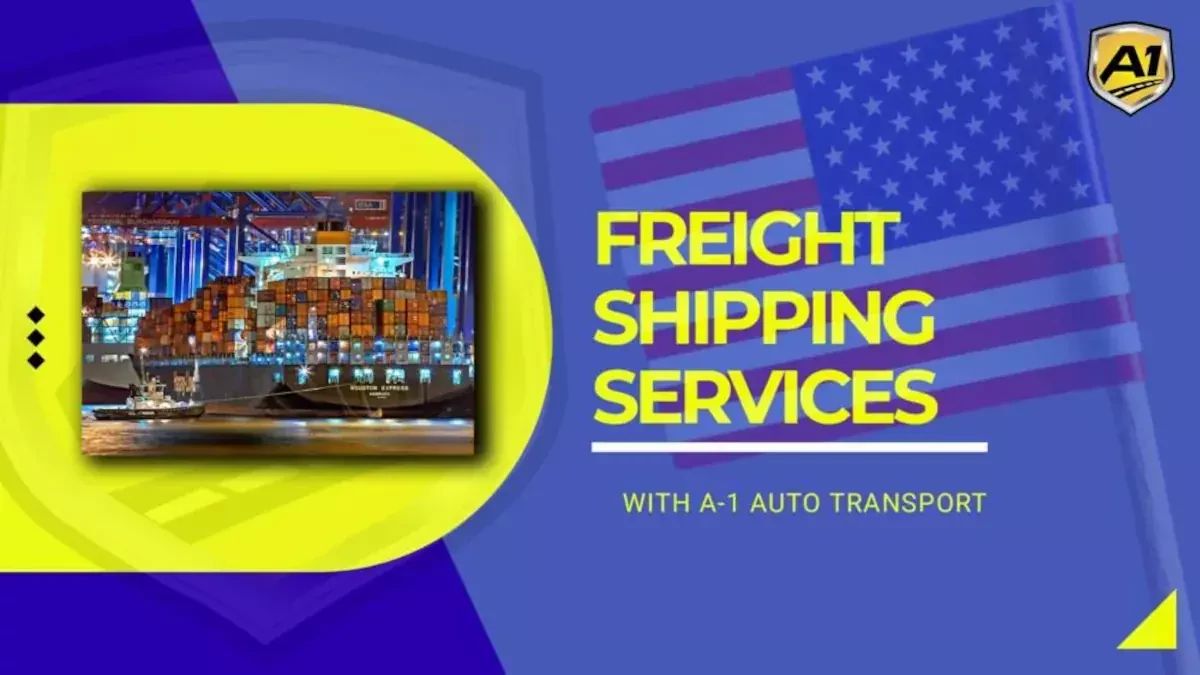
Freight Shipping & Heavy Cargo Transport
We also offer moving for those who need a service that doesn't fall under our other services. A1-AT shifting provides more services and is not limited to vehicles or certain types of equipment—there are no size or weight restrictions.
Types Of Logistics
- LTL—Less Than Truckload Carriers: The LTL class can provide warehousing and distribution services for your cargo and business. This service offers the advantage of hauling small quantities at a time since it will make multiple stops on the supply chain to the same destination.
- FTL—Full Truck Load Carriers: This type of class specializes in moving up to 53' semi-trailer loads or full truckloads (FTL) for one customer or business outfit. It offers the advantage of moving larger quantities simultaneously but will only go to the destination once.
- TL - Trailer Load Carriers: These companies specialize in hauling a single trailer load, either one or two containers. They offer the advantage of moving larger quantities at a time and will go to their destination more than once.
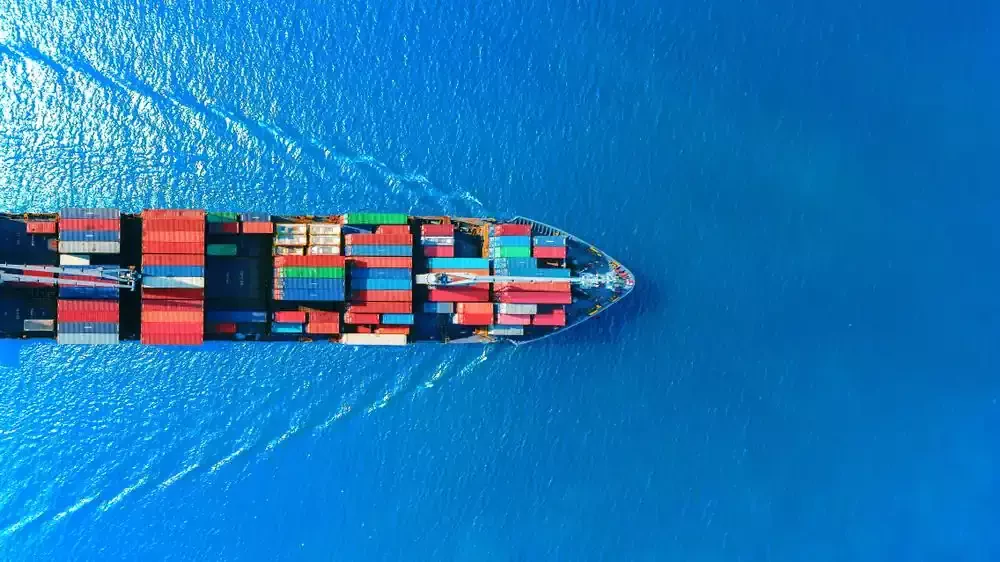
Choosing The Best Firms
The factors below will help you choose the best relocators for your needs:
- Vast Network Coverage—Before choosing, Ask which services they offer and how far they travel to pick up or deliver. Will it be in your domestic area? Also, ask the experts if there are any restrictions on the goods and destination (e.g., hazardous materials).
- Transit times - Ask how long the hauling requires to arrive at your location, and you determine which service is best to save time.
- Range of services—The best firms offer services, such as open and enclosed carriers, time-definite schedules, and expedited supply chain deliveries. This allows them to adapt their plans to meet individual customer needs. Check if the heavy items can be hauled domestically by sea, air, or land.
- Reliability and communication - You want to be able to communicate with the companies throughout the process. What are their hours of operation? Do they have an emergency phone number you can call 24/7 if necessary?
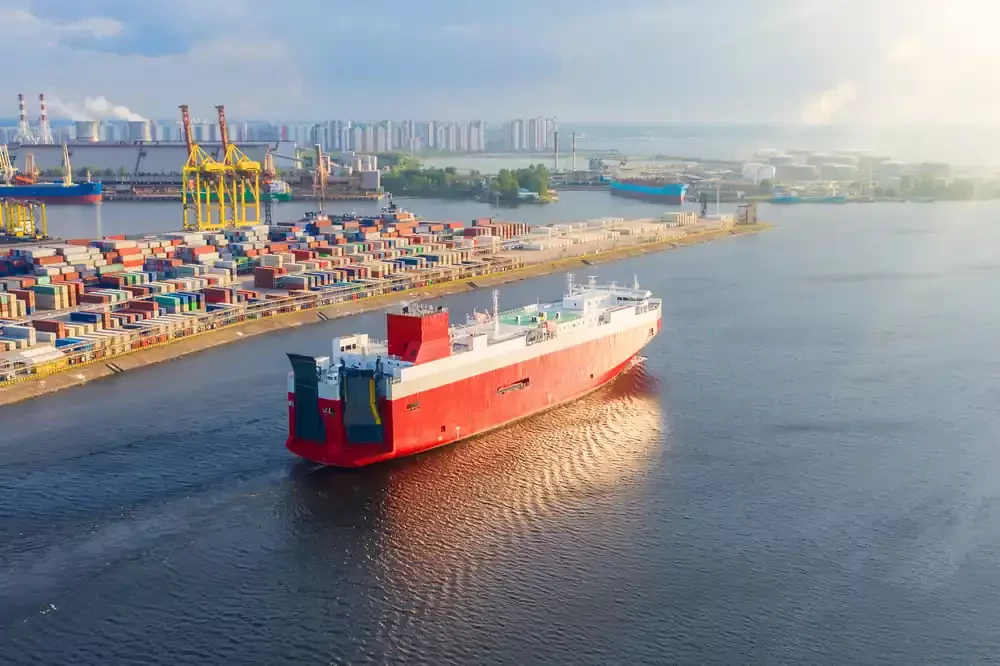
Dispatching Prices
The cost depends on several factors, such as the distance your goods travel, the class you choose, and how quickly you need them.
Rates & Transit Time Examples
Shipping To/From | Cost | Distance | Transit Days |
---|---|---|---|
Los Angeles to Las Vegas | $115 | 270 miles | 2-4 days |
Chicago to Memphis | $255 | 530 miles | 2-4 days |
Atlanta to Detroit | $270 | 725 miles | 3-5 days |
Denver to San Diego | $300 | 1080 miles | 4-6 days |
San Jose to Dallas | $595 | 1275 miles | 4-6 days |
Phoenix to Seattle | $680 | 1425 miles | 4-6 days |
Atlanta to Phoenix | $470 | 1845 miles | 5-7 days |
Detroit to Las Vegas | $560 | 2015 miles | 6-8 days |
Seattle to Memphis | $770 | 2285 miles | 6-8 days |
Portland to Miami | $1210 | 3255 miles | 7-9 days |
- *Pricing and times to relocate are estimated. They can vary depending on the season and what you are moving.
- *Rates are based on a cargo of 200 kg.
- *Call us for specific date and time-sensitive requests.
Here Are Some Of The Many Items We Shift
- Mining supplies & equipment
- Construction Equipment
- Industrial Supplies
- Oversize loads & heavy haul
- Boilers
- Turbines
- Refrigerated
- Containerized cargo (intermodal)
- Less than a truckload (LTL)
- Full truckload
- General Hauling
- Distribution services
- Expedited delivery
- Warehousing & storage
If you have questions about packing and moving anything not mentioned here, especially if you've had trouble finding a suitable option, don't hesitate to contact us to learn more about how we can help. Call us at 1-888-230-9116 to learn more about how we haul and get an instant price quote using our online form.
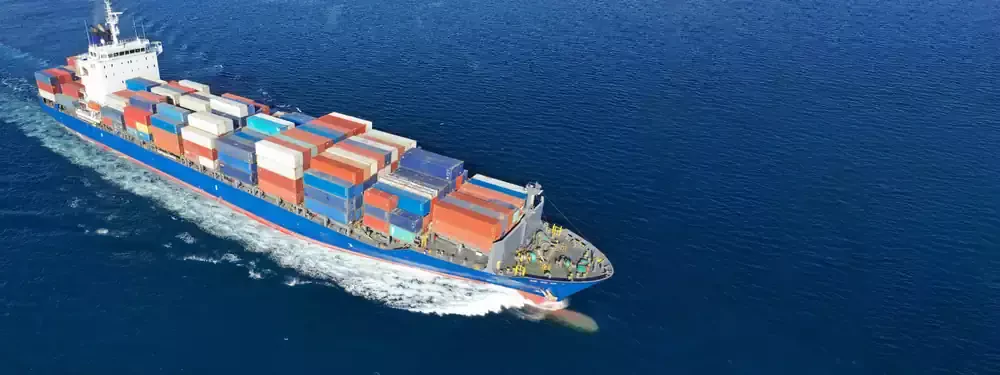
Conveyance Modes
The right relocation equipment is a key part of the process, especially for companies and heavy-duty hauling. Various class-shifting options and equipment are available, but some require special handling, while others are easier to manage. The section below outlines the main Haul service types, key differences, and moving requirements.
Most Load loads within the U.S. are delivered using a flatbed truck. The specific type of trailer used depends on the cargo being hauled and its final destination. However, this covers most relocations within the continental United States and other countries' borders.
While less common for private haulers or small businesses, some can and still are moved by rail. It is less common because most containers can be easily moved by truck, making tracking trains redundant unless there is enough cargo to make it financially worthwhile for the party moving.
While air freight is more expensive, it is still an option, even for heavy Goods and large ones. Typically, air Cargo is used when a shipment must reach an out-of-the-way or otherwise difficult location that may not be as accessible by haul, train, or truck.
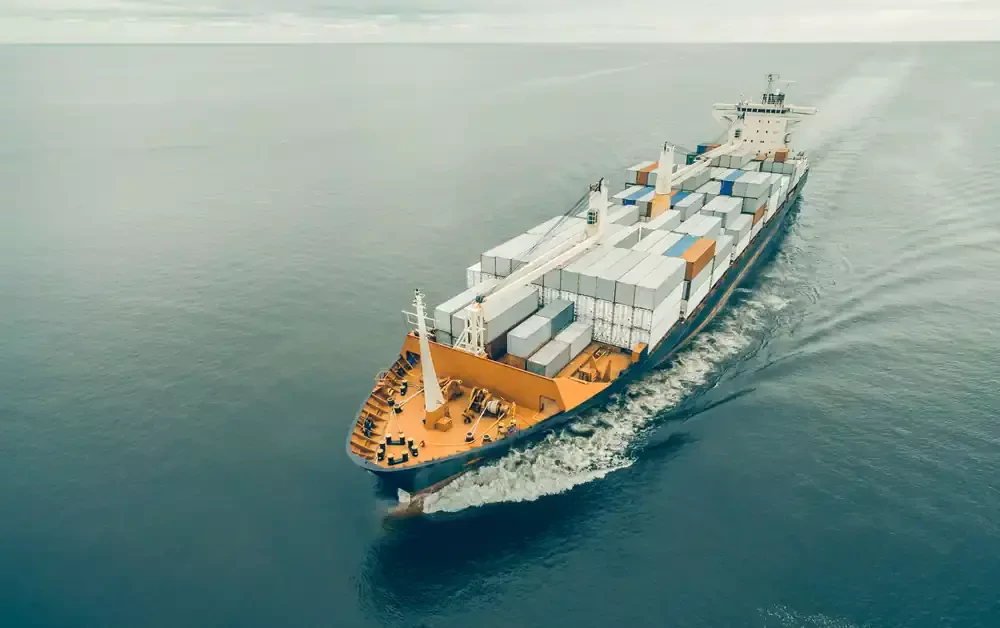
Preparing For Delivery
- First, choose how much space your shipment requires (a 20' or 40' container).
- Then, choose the type of vehicle you want to shift.
- Lastly, plan your pick-up and drop-off time.
Are you looking for the best companies near you? Here is how to move using us.
Request Our Goods Transit Quote.
Our company will provide pricing based on weight or volume and moving distance.
Prepare Your Goods
Ensure you have all the necessary paperwork for a legal move (proof of ownership, registration, driver's license). Also, remove any personal belongings from your car before the delivery.
Book A Pick-Up Time When You Haul
We will need specific instructions on where and when the Load will be ready for pick-up.
Collection
The timeline between scheduling and arrival varies depending on where you are in our terminal locations.
Do you need services in the U.S. to be hauled domestically or internationally? Call us today at 1-888-230-9116 to learn more about the process or to request a FREE, no-obligation cost estimate from the experts! With some basic information, you'll have a price quote with the best rates in minutes!
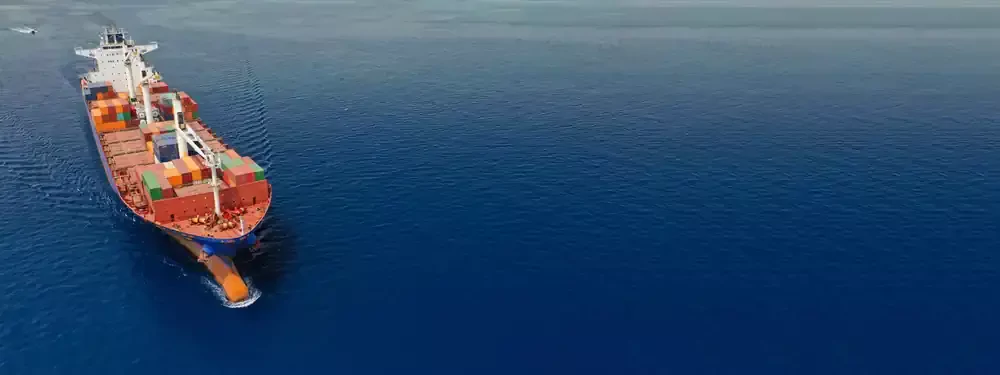
What Our Customers Say About Our Services?
I’m a small business owner and had never hauled anything over 50 pounds in my life, with this being my first load. I was out of my league when I came across A1-AT, but their helpful website and free quote calculator made my load very easy and got me a great rate. Highly recommend them for needs. - Dimitry L
Informative website, excellent customer service, and a great way to get the most competitive rates anywhere you need it to go. I’m a seasoned vet regarding shipments, and A1AutoTransport.com is my go-to website for all my needs. I’ve never been let down. - Andy D
Moving With Us
Our competitive edge, however, is that we provide a goods service specifically designed to meet your requirements. You can trust that your goods will be delivered quickly and affordably since we prioritize thoughtful route planning and adaptability. We always use cutting-edge hauling and tracking technology, including real-time satellite monitoring. One of our top concerns is ensuring your goods' security and safe arrival.
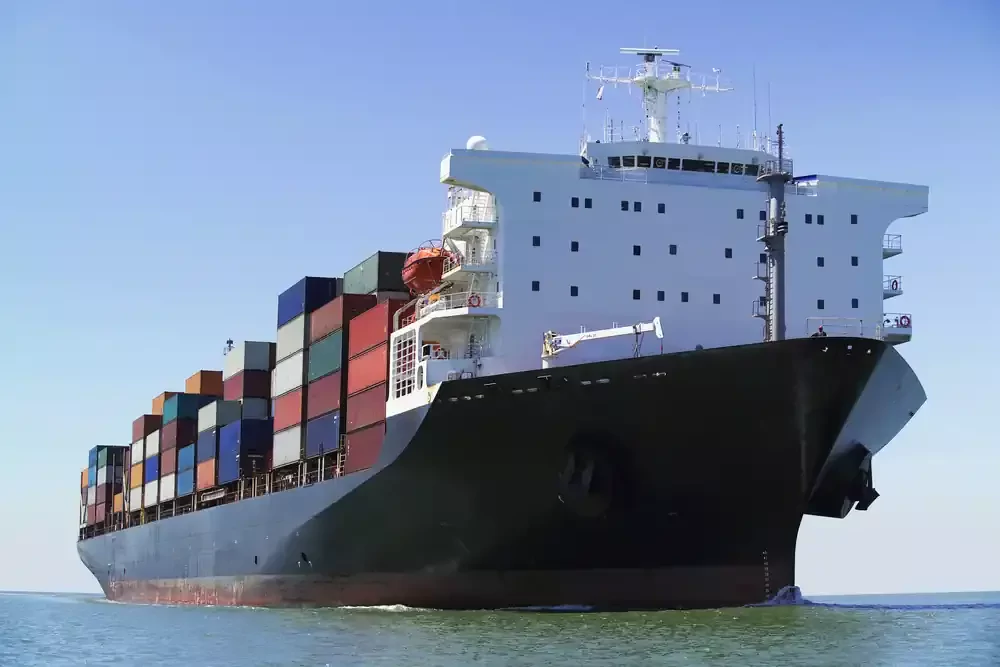
Our Services
In today's highly competitive economy, you need to be confident that you're hiring a shifting service that will be able to provide you with fast and effective hauling. The company should provide the best costs and services, NEVER be late, and ALWAYS coordinate logistically to your needs. Our extensive carrier relationships and dedicated customer service team will ensure this happens.
We offer the following services:
LTL (Less Than Truckload)
In most cases, you will not need to fill up a truck with Load that's the c. IFASE for you, our compressive services are the perfect solution. Whether for residential or commercial conveyance, we'll work with you to plan how to relocate, no matter how small, in the most cost-effective yet efficient way possible. Our network of multiple carriers specializes in LTL carriage, so you can be assured that you'll get the best service for the best price possible.
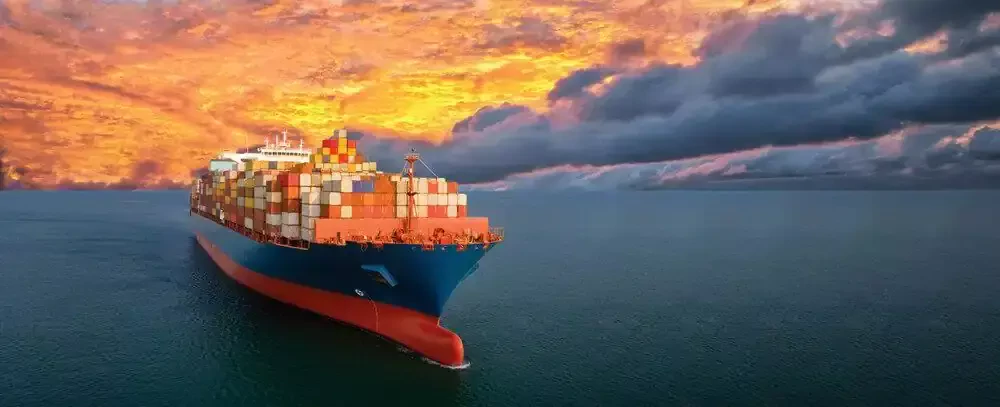
FTL Cargo (Truckload)
Sometimes, you will need TL if you have a huge load. In other cases, you may be hauling an extremely delicate load that needs its truck. Whatever the case, our services will only use the best truckload carriers to get you the best available on the marketplace.
Intermodal
This is the perfect option for those who need international moving. Your load load can be moved through multiple processes, and it will be securely handled and delivered here. We assist you with all the duty and customs requirements of international conveyance, resulting in less stress, better access, minimal delays, guaranteed delivery, and even cost savings.
Here are some of the services we offer our dispatch clients:
- Dry van
- Flatbed
- Long haul
- Small trucking
- Top trucking companies in your area now
- Air Cargo
- Expedited delivery
- Ship to and from Canada
- Temperature-Controlled
- LCL (Less than Container Load)
- FCL (Full Container Load)
- Intermodal Shifting Containers
- Import/export logistics
- Ocean Moving
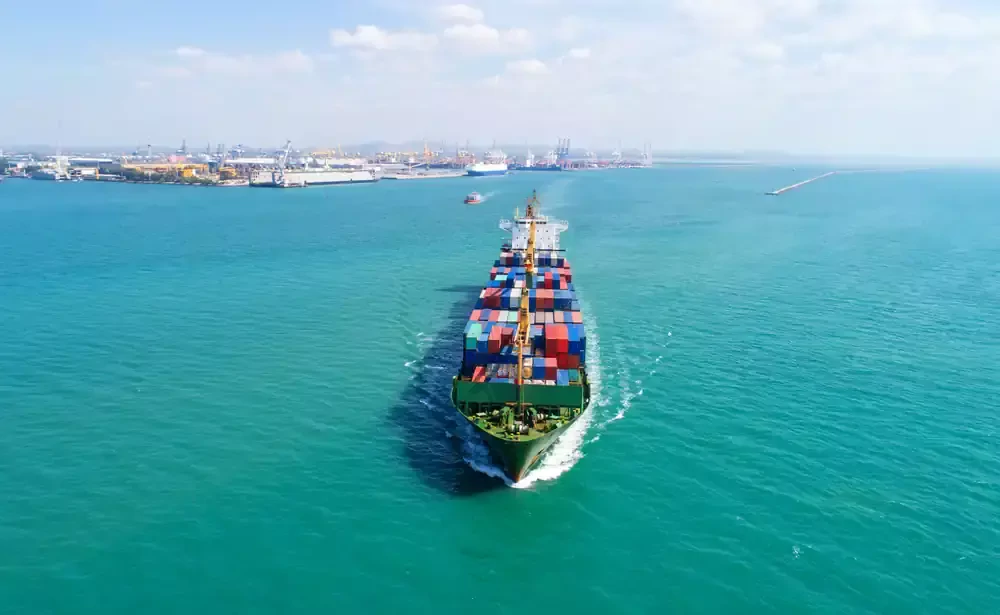
Why Choose Our Services?
- Industry-leading experts from our customer service team
- Efficiency in shipments that results in significant COST SAVINGS
- A simple and fast booking process in which you can ALWAYS speak to a customer service representative
- The latest GPS tracking technology allows you to track and receive real-time updates on what you haul.
Contact us today to speak with a customer service representative to learn more about what we can offer to meet your requirements. We will also provide you with a FREE QUOTE.
Frequently Asked Questions
What's the difference between consignment and cargo?
Cargo is transported goods by a freight company. Freight is the term used for the payment of goods, i.e., "freight bill." While there is a difference between the two, they are both used when referring to shipping goods.
What is consignment forwarding? What is the difference between a mover and a Cargo forwarder?
Freight forwarding is a third party that takes care of all the logistics and business involved in getting your package to its destination.
Shippers are persons (or freight shipping companies) who transport their personal goods. In contrast, a package forwarder is a third-party company, which can be your considered Haul option.
How do you determine my consignment rates? Is it by size? Weight? Both? If you give me a quote, how long will it be good?
Cargo quote is an estimate given called a "dynamic spot quote." The more exact shipment details you provide, i.e., weight, height, origin, a destination address, etc., the more accurate an estimate is.
There are a few factors to include when calculating costs of shipping cargo:
- The dimensions of your cargo
- The weight of your cargo
- The destination of your cargo
- The value of your cargo
- The speed of delivery required
- Will there be any custom clearance required?
- Freight class opted for your shipment
*Shipping internationally is another factor
In the shipping industry, most quotes are only good for one day because of the dynamics. So, your best bet is to have all your exact shipment information ready when getting a quote and be prepared to ship at a lower price.
What kind of carrier transits my consignment?
Intermodal carriers use standardized cargo units such as containers and semi-trailers that are moved easily across different modes of transportation (ships, trucks, air, or train).
Most shipping within the U.S. uses flatbed trucks, and the type of trailer used depends on the type of goods hauled.
The other types of transport methods, ship, and air are not as popular for private shippers because they are expensive. After all, most shipping freight in the U.S. can be handled by truck.
Depending on what you want to haul, we have vetted carriers that fit your needs best.
Will my Load be on a truck with other items? How do you guarantee safety with your load service?
Depending on how much Cargo you have, your goods could be on a truck with other items. It can be a single shipment, but international shipments may require multiple carriers to save money and time.
When a truck travels with a partial truckload (PTL), partial truckload freight fills the gap between less than a truckload (LTL) and full truckload cargo.
If your shipment doesn't fill an entire trailer, it will be considered partial truckload freight (PTL) and put on a truck with other cargo.
To ensure that your items are safe during transit, they are packaged (plastic, bubble wrap, etc.) and maneuvered onto crates and pallets to handle your things safely.
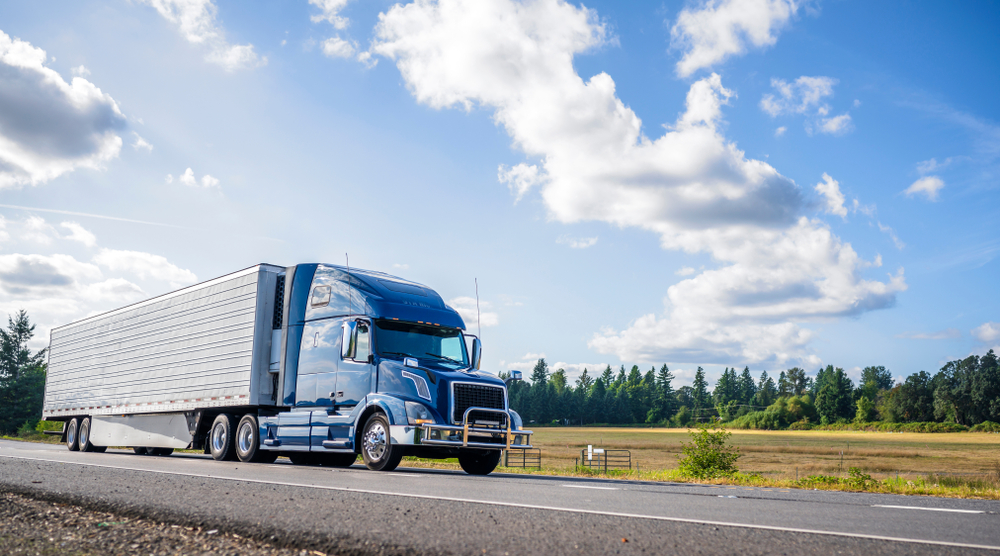
Do I need to have insurance? Will my homeowner's insurance work or is there another way?
Some of our customers confuse freight and cargo insurance, so first to clear up the difference – freight insurance protects the freight forwarder or carrier. Cargo insurance protects the sender of the goods, you!
Cargo insurance is essential if you want coverage for the total value of the bulk goods in the event of loss or damage such as faulty loading/unloading, accidents, fire, theft, heavy weather, and other natural disasters.
Cargo insurance is usually up to you, the sender, of the shipment. However, some freight carriers will arrange cargo insurance, coordinate with the insurance provider, and get the insurance policy for you.
Homeowners insurance will not help you with freight shipments.
Am I responsible for packaging my load? If not, how do Load firms package?
Some forwarders do offer packaging services. These services may be done in-house or outsourced to an external company using various materials such as packing peanuts, loose-fill packaging, bubble wrap, blankets, and plastic wrap.
If the forwarder doesn't offer these services, you, the shipper, must pack your freight at land locations. If you pack your cargo, it is your responsibility to provide access and prove that it was delivered to the carrier in good condition and packaged correctly before transporting. When this is complete, it becomes the carrier's burden to prove it wasn't negligent in case of damage.
Am I able to speak with someone while my Delivery is in transit? I'm not great with the computer, so will there be a human being I can talk to during cargo delivery?
Yes, most freight brokers and carriers have operators standing by, ready to speak with you about your freight shipments before and during transport. Most also have online help if you're comfortable working with a computer to track your Cargo transportation.
Before a company picks up your Load, you'll have a phone number to call and an order or business quote # to give for reference. In addition, you will be given a Bill of Lading & Freight Bill with a contract # to refer to if you have any questions or concerns during transit.
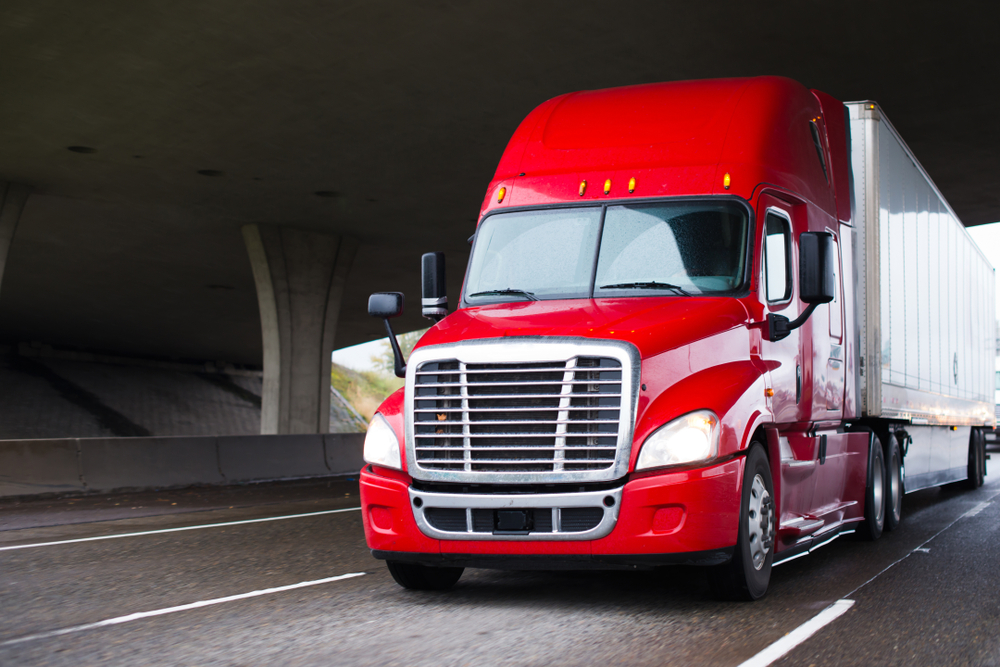
How far in advance of my delivery required date should I make a transit reservation?
Making a reservation to ship cargo depends on your shipping load and how much of a truckload you're using. If your shipment is considered partial truckload freight (PTL), the shipping date is when the hauling company can place it on a truck.
There are generally no set dates or times for the transportation. Instead, what space is available on trucks when you need to ship and from where. While this may not be the most satisfying answer, it is the truth in freight shipping business.
Whether you're moving your household items across the country, an office load of equipment, or one item, it will be up to the trucking company or broker to help you determine what they can do.
To be prepared to make a shipping reservation at the best rates, be sure to have all the information available when you contact the company, including pickup location, destination, size, weight, and packaging needs.
Are delivery dates guaranteed for your cargo dispatch services? I have a deadline for delivery.
Many cargo carriage companies will guarantee delivery based on locations. What could keep delivery from being assured could include hazardous and oversized cargo and shipping cargo to remote areas.
Depending on your situation, delivery can be guaranteed, but be sure to discuss your details with the carrier to understand your needs and ship your cargo accordingly. Plan to get a pricing quote in advance so you don't end up paying more money to ship cargo at the last minute.
I live on a narrow road. What happens if your truck can't get to my house?
Residential pickup and delivery depend on the freight company you use.
Some cargo shipping companies will require that you have the cargo palletized on the street so the driver can quickly get the load on the truck, while other freight shippers will work with you to pick it up from your residence; it depends on the driver.
When finding out about residential pickup and delivery, ask whether you'll need a liftgate to help get the freight on or off the truck. Some freight shipping companies will charge liftgate fees, and some don't.
While this can't be a definitive answer, know that a load broker or carrier can address your unique situation for pickup and delivery. Although shipping load may require additional equipment or fees, pickup and delivery conditions can be addressed satisfactorily.
