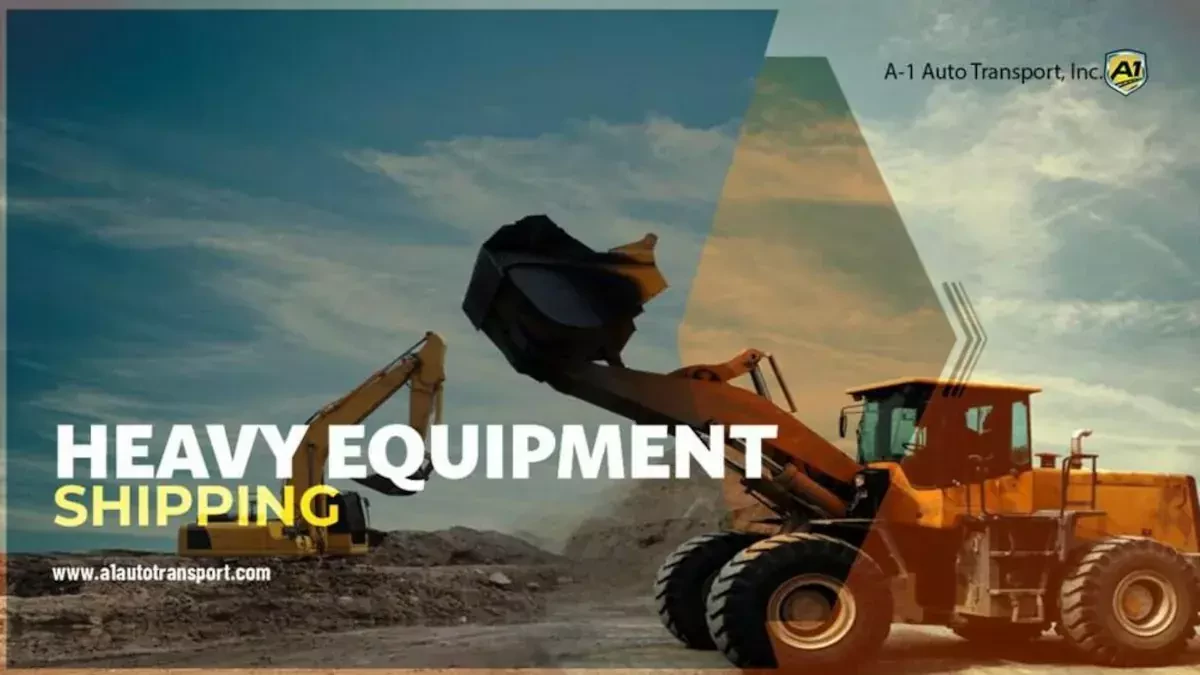
Understanding Heavy Equipment Transport
The global heavy supplies moving industry is valued at approximately $42 million, and more than 95% of weighty shipments are moved by sea. We don't just transport your vehicles; we also assist you with moving any item, ranging from tractors to cranes.
Your machinery is a crucial component of your spreader company's success and represents a significant investment made by your firm. Hence why reliable heavy equipment hauling is very important.
Therefore, it is essential to ensure careful handling during massive materials haulage. Bulky equipment conveyance refers to shifting large instruments and vehicles. This type of load is commonly used in industries like construction, mining, and agriculture.
Below, you will find information about the most commonly moved machinery models in the trucking industry, along with some basic information you will need to get an estimate and tips on how to approach the process.
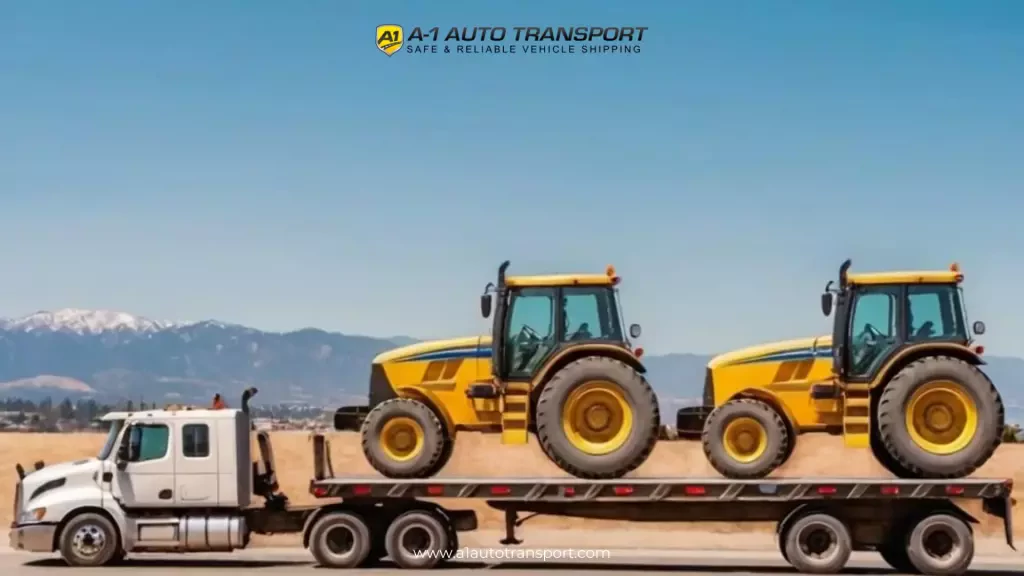
Examples Of Pricing & Time To Ship
Shipping To/From | Cost | Distance | Estimated Time In Transit |
Gilbert to Durham | $3743 | 2139 miles | 6 - 8 days |
Pittsburgh to Saint Paul | $1507 | 861 miles | 3 - 5 days |
Newark to Cleveland | $791 | 452 miles | 3 - 5 days |
Minneapolis to New Orleans | $2137 | 1221 miles | 4 - 6 days |
Bridgeport to Raleigh | $987 | 564 miles | 3 - 5 days |
Albuquerque to Atlanta | $2446 | 1398 miles | 4 - 6 days |
Memphis to Oklahoma City | $815 | 466 miles | 3 - 5 days |
Seattle to Columbus | $4790 | 2737 miles | 6 - 8 days |
Apparatus Hauling Near Me
Are you in search of movers in your area? Moving large items requires the expertise of professionals in the heavy equipment transportation industry. Whether you need to transit cargo across the country or overseas, oversized deliveries can be fulfilled to any destination with the help of reliable equipment freight solutions.
General Factors
Weight, dimensions, and regulations are crucial in determining the forwarding method for heavy transport oversized loads.
Various manufacturers and industries rely on heavy machinery services to haul Implements such as farm instruments, tractors, hydraulic forklifts, cranes, bulldozers, industrial tools, engines, construction apparatus, and many other goods. We have recently helped transport different types of apparatus, including those with attachments, both in the United States and overseas.
- Conveyance for Tractor combines & farm materials.
- Backhoes and excavators
- Industrial Apparatus
- Bulldozers haul
- Dump trucks
- Forklifts
- Hydraulic haul
- Engines haul shipment
- Track loaders & graders
- Pile drivers of haul
- Large trucks & vehicles
- Transport vehicle
- Trenchers & scrapers
- Engineering & agricultural tools
Contact Us
We can also move just about anything else. If you have any questions about your conveyance needs, contact us, and we’ll be happy to help you or point you in the direction of someone who can help!
Our Bulky Transit Insurance Policy
Because weighty instruments insurance covers damage to the materials during conveyance, asking customer support about our insurance policies for hauling are asking about insurance. Whether you work directly with a broker or the carrier, you should ensure the carrier's tools insurance covers any potential damage to your hefty tools during transit. It's also essential for you to understand how damage claims are handled.
For such information, you will have to communicate with the carrier directly. If you are working with a broker, be sure the broker carefully selects carriers with adequate equipment insurance coverage and adequately handles damage claims.
Whether you hire us to transport your oversized cargo as a carrier or a broker, we can assure you that the insurance coverage will be adequate to cover any damage to your rigs during conveyance. Furthermore, we ensure that should you need to submit a damage claim; we will assist you at every step and ensure your claim is handled promptly and correctly!
Hire Reliable Hauling Solutions Near Me
Oversized equipment moves may involve securing necessary permits, coordinating logistics with logistics agents, cargo insurance, special handling and ensuring compliance with local laws and regulations. Finding a reliable and safe apparatus moving firm is essential if you require a haul.
Search for "Heavy Machinery Hauling near me" on Google to find one. This will help you locate companies specializing in secure cargo using specialized trailers such as step-deckor flatbed trailers using the right trailer for your heavy load.
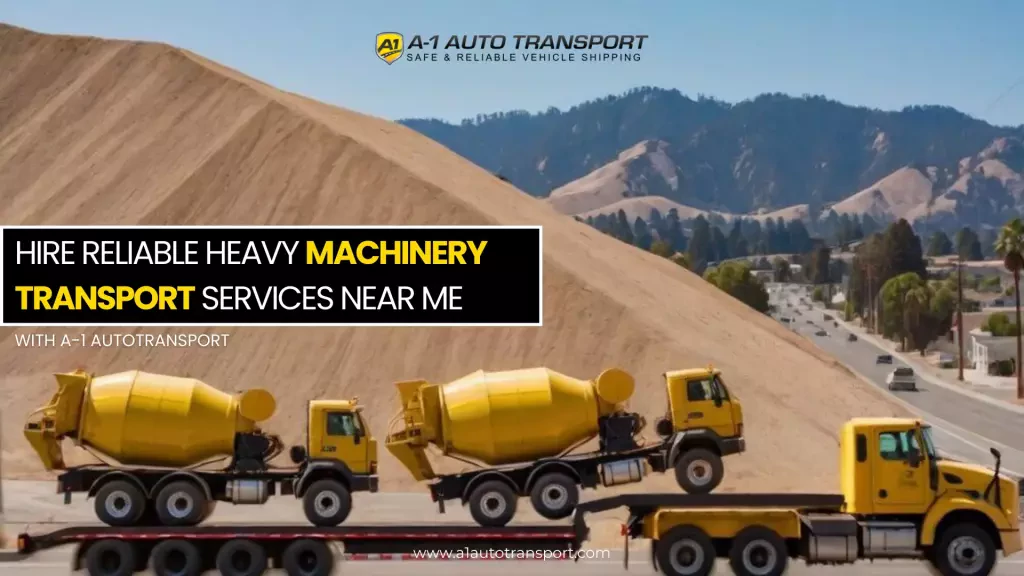
Best Fit
You can read reviews from other customers to determine which firm best fits your needs. This will give you an idea of the transportation company or transportation services reputation, experience, pricing, and more. Once you have a list of potential load carriers, you can contact them and ask questions about their products, pricing, and freight insurance.
Professional heavy apparatus movers will explain all your options, including container sizes and insurance information, and provide free quotes for moving your instrument. Some firms even have online calculators that can give fast estimates based on rates per mile, weight, and size.
Fortunately, the price for hauling machinery is known as cost-efficient, and you can expect to receive competitive pricing from reputable businesses.
Why Use Us?
The worry of complying with state requirements will be removed if you have a reliable and trustworthy conveyance enterprise like A1 Auto Transport. This covers the paperwork required to obtain the licenses to send big loads. A reputable conveyance firm like A1 Auto Freight will complete the forwarding procedure from pick-up to delivery.
This kind of arrangement is essential to the success of your project. We will also take care of the legalities and obtain your required permits. In addition, you will have more time to concentrate on other crucial matters because you will know that your priceless item is in the capable hands of shifting professionals.
Benefits Of Us
- Removes The Initial Cost Of Buying Delivery Trucks:
In the long run, you may save a lot of time and money by employing a hauling business like A1 auto freight, as they promise that all maintenance and repair costs will be covered.
- A Company That Transports And Drives Has Greater Experience
Well-known hauling businesses like ours employ drivers with extensive training and expertise who are familiar with transmitting nuances. They will evaluate the options and select the fastest, safest, and best routes to ensure your cargo arrives at its destination on schedule and in good condition.
- Obtaining Escorts and Trucking Permits Is No Longer Your Issue
Permits and paperwork won't be an issue if you decide to work with A1 Auto Carriage. It could be challenging to determine for yourself whether or not your burden is oversized. Fortunately, we will assist you in determining its size and choosing the appropriate trailer, as we are the top shipping company. Our skilled logisticians will assist you in obtaining the escort cars required for safe and authorized transit if your load is more extensive than usual.
Some Reputable Manufacturers Include:
Texas, Hawaii, California, Florida, and New York are central U.S. states with ports that accept and handle these oversized loads. It takes specialized towing equipment, state-of-the-art carriers, and haulers to get large cargo containers from movers to their destinations.
What Is Considered To Be Gadgetry?
Heavy machinery is a broad term that refers to a wide range of devices used in various industries. This gear is defined by both its weight and size. Some common examples include:
- Tractors
- Forklifts
- Cranes
- Industrial
Machines in this category may require specialty carriers instead of traditional flatbeds. Fortunately, we can facilitate your moving needs by connecting you with one of our reputable kit movers near you.
Cost And Time To Move Examples - How Much Does It Cost?
Distance | Cost | Estimated Time In Transit |
0-200 miles | $4.00 - $5.00 per mile | 1-3 days |
200-500 miles | $3.50 - $4.00 per mile | 2-4 days |
500-1000 miles | $3.00 - $3.50 per mile | 3-6 days |
1000-1500 miles | $2.50 - $3.00 per mile | 4-7 days |
1500 - 2000 miles | $2.00 - $2.50 per mile | 5-8 days |
2000 - 2500 miles | $1.50 - $2.00 per mile | 6-9 days |
2500+ miles | $1.00 - $1.50 per mile | 7-10 days |
*Prices and times for large transport are estimated. They can vary depending on the season and the supplies you transmit. Get your provider a load and easy dispatching estimate using the form above and transport heavy equipment or industrial equipment with proper loading and careful planning today.
You can give us your email address and we will provide a real-time quote for overweight loads.
The Influence Of Size And Weight For Freight Shifting
Remember that the size and weight of your implements are the primary factors determining the overall shipment cost. Due to dimensional constraints, some materials may need to be disassembled before the movers load and unload them.
Additionally, the size and weight of your instruments may affect the hauling options available for overseas destinations. If you're dispatched overseas, a transit method for lift-on, lift-off tools may be more suitable than a flatbed truck.
You can find more information on shifting options and a guide to finding the weight of construction supplies in the resources section at the bottom of the page.
If you have any questions about a load, need guidance, or would like a cost estimate for cargo, don't hesitate to contact us today or use a quote calculator to get an estimate instantly.
We offer peace of mind, oversized load permits, fast delivery times, many load options, and the lowest rates for your instrument delivery needs.
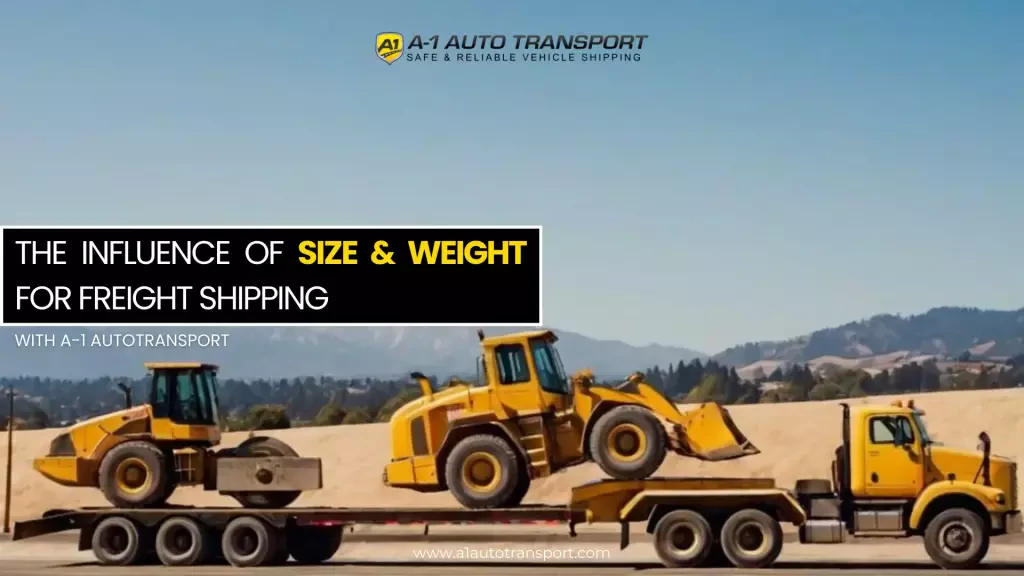
Accessing Dispatching Requirements And Restrictions
Two key ingredients to a positive experience are expertise on behalf of the haulage company doing the work and assurance that you’re in good hands even if accidents occur.
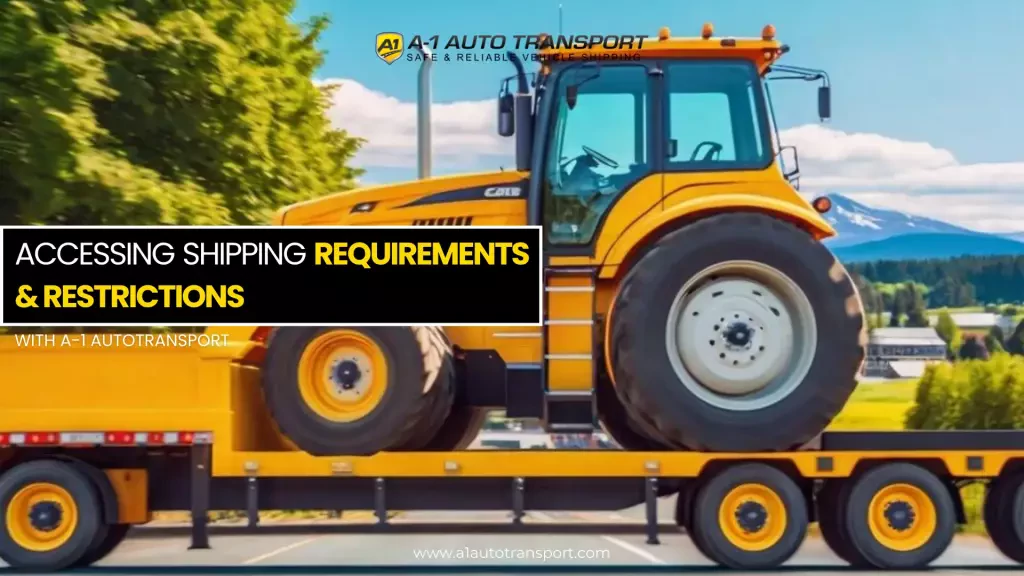
Relocating Insurance
It should be pointed out that oversized loads often come with a higher cost than regular loads, but they are a crucial part of many businesses.
Suppose you must move gear, construction materials, or other large machinery items in potentially challenging weather conditions. In that case, working with reputable transport providers specializing in this service type with best practices is essential. These haulers are required by law to have a certain level of insurance to ensure the safety measures of their items is propertly planned for.
While it can be challenging to find this information online, most haulers will be happy to provide it if you ask.
Additionally, the hauling contract typically includes insurance coverage as well.
The Expertise Of Your Assistance Provider
Having expertise is crucial when in the business of hauling oversized items. It requires attention to detail and the appropriate experience of qualified transport specialist service providers.
For instance, a shipper which higher risk assessment who frequently moves combines or other machinery across the state using a step-deck or other special trailers may not be the right equipment option if you must transport a heavyweight skid steer long-distance to Canada or across the country.
Repositioning Regulations In The U.S.
In the U.S., the Environmental Protection Agency and Customs and Border Protection have their requirements for oversized item shifters regarding emissions, documentation, fees, import, and export.
Consult with government websites or your service provider if you’re curious about the details, but the most reputable dispatchers will handle these matters.
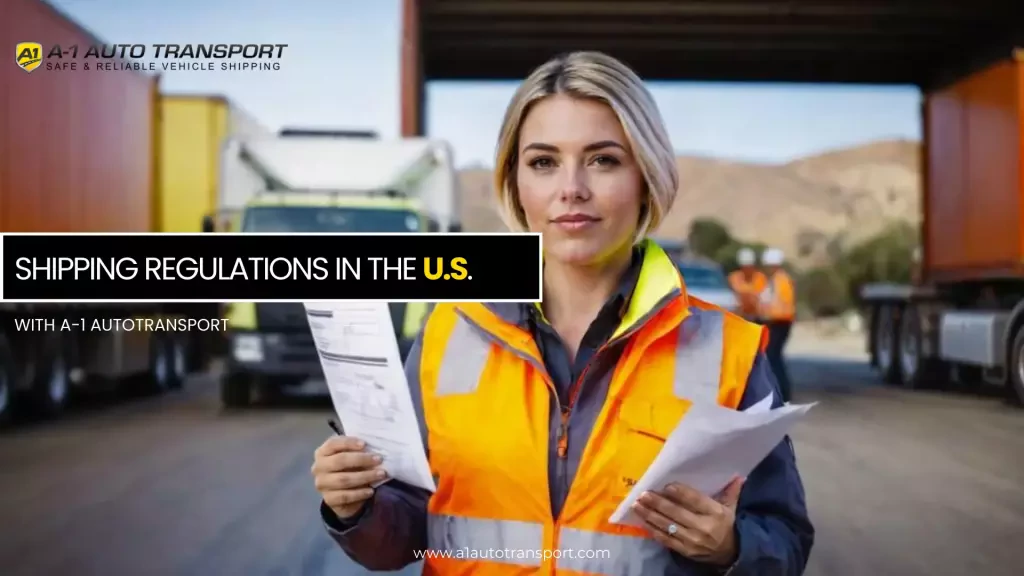
Choosing The Right Delivery Firm
Depending on your destination, various professional service options are available if you need to haul oversized loads or a different heavy equipment shipment. Not all oversized load trucking solutions offer the same options, but you can move your cargo by aircraft, heavy-lift ships, flatbed trucks or trailers, or containers.
Many services offer different options to suit your needs. It's essential to consider the moving machinery type and whether it requires special care or hauling instruments. Don't hesitate to ask haul trucking companies if they offer any unique benefits.
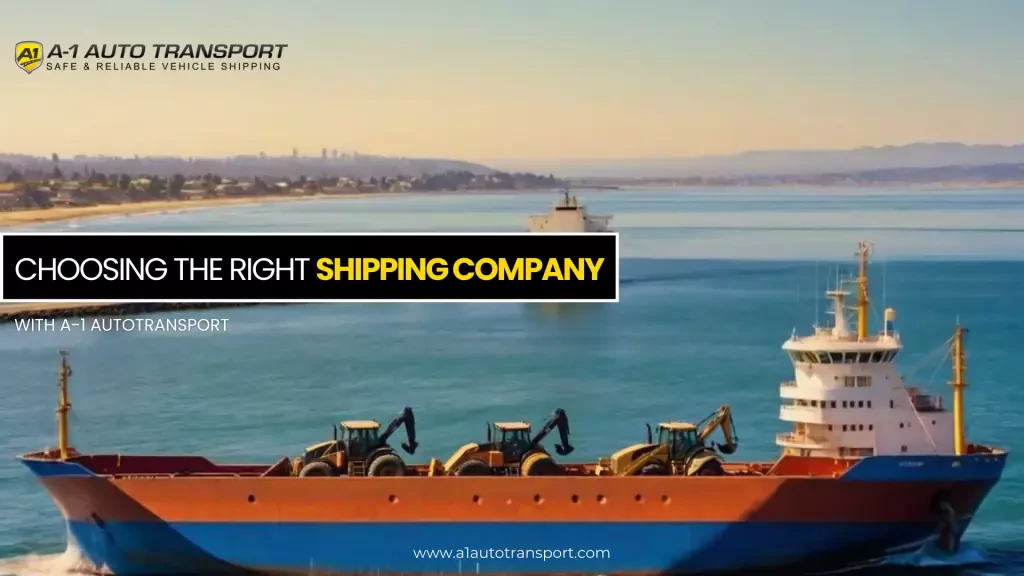
Things To Consider Before Arriving Movers
On the day of your scheduled movers' arrival, ensure the area is clutter-free for the loaders. They'll need adequate spaces to work safely and ensure maximum performance. Providing the movers with this security and clearance is worth spending time on.
Once the shipment leaves your property, it is protected by insurance held by the freight hauling company as it makes its way to its destination.
The movers can transfer your load to another hauler during the trip.
Overseas Hauling Methods
Roll-On/Roll-Off – The RoRo method is a popular form of materials relocation delivery made to a country overseas. A flatbed hauls vehicles such as motorhomes and industrial machinery. Remember that there are some height and weight restrictions on this method.
Flat Rack Heavy Haulers – This haulage method delivers boats, RVs, and other items on a flat rack secured to a relocate.
This open-air method is favorable due to its cheaper best deal rates and ability to dispatch a broader range of cargo.
Container – This option is ideal for transmitting gadgetry when your cargo can fit into a large movement container. It offers your gadgetry more protection against weather conditions.
Lift-On/Lift-Off – The LoLo method is best used for inoperable vehicles, engines, farm materials, and other tools. A crane lifts your cargo onto a shift to move the oversized load.
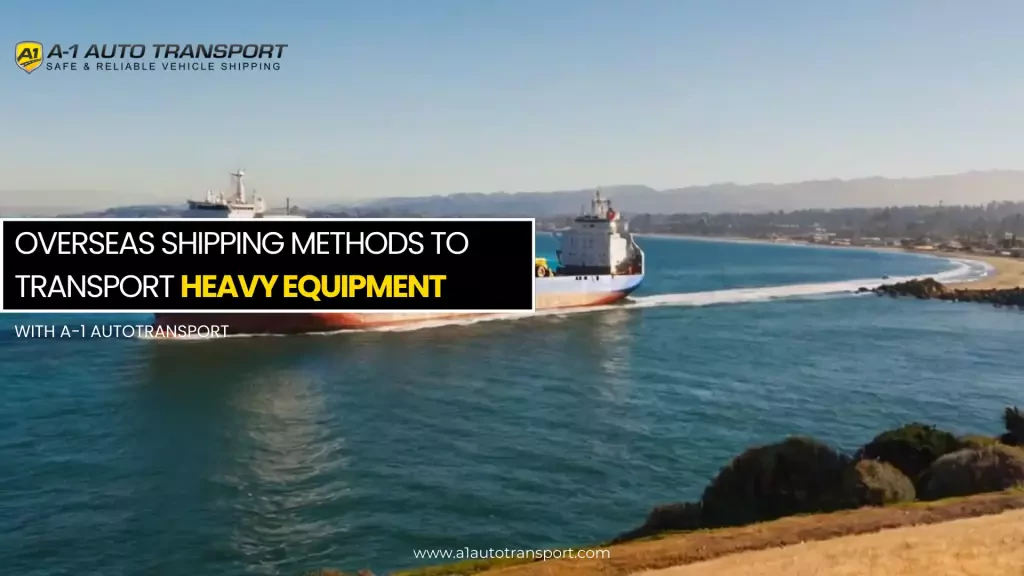
Things To Know Before You Transit
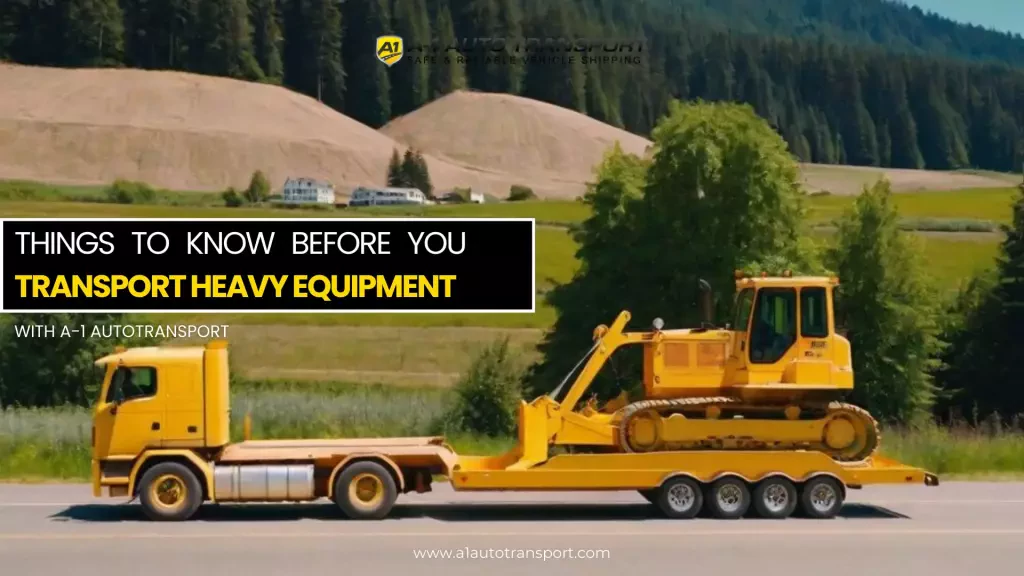
Generally, transporting machinery is a smooth and efficient process. With that being said, there are a few things you need to know when arranging your freight shipping services. These include:
Dimensions For Conveyance
It is essential to have precise measurements of your heavy hauler's freight. Our team requires this information to assist you in arranging your transit services. Inaccurate measurements can lead to expensive delays and oversized loads.
If you are uncertain about how to measure your machinery, please do not hesitate to contact us for assistance.
Required Haulers Loading Cargo
Does your oversized load require any specialized loading? If so, make sure to discuss this with our team in advance. This allows us to pass that information on to the carrier and avoid any issues with your machinery order before pickup.
Permitting Move Regulations
You will need special permits to move your apparatus to another country. Oversized equipment that exceeds the specified weight of the equipment limits will also require permits for oversized loads for fleet management and state regulations.
Failure to obtain these permits in advance may result in delivery delays or affect the pricing for cargo freight insurance.
How To Prepare For The Hauler Load
Here are a few tips for you to make sure you are ready for the hauler load:
- Please ensure your unit is ready to be loaded onto the truck when the driver arrives. This includes retracting booms and positioning your delivery to fit safely on the flatbed.
- Depending on where you want to dispatch the unit, you may also need to remove the scoop or bucket. Some states have made it illegal to move your shipment with a scoop or bucket attached.
- It is essential to cover the exhaust stack to prevent unwanted debris from entering and damaging it. Additionally, disconnect the battery to prevent it from being drained if lights or other components are accidentally turned on during conveyance.
- Before moving your apparatus, make sure that all doors are secured. If they are not, they could catch the wind and become damaged during cargo.
- Lastly, it is recommended that your cargo is washed. Dirt and debris can obscure tie-down points and make it challenging to inspect if it is foul.
Types Of Cargo
Freight Information - Learn More About Freight Supplies Transit
- How to ship industrial materials
- What is an oversized load
- Gear haulers for hire
- Materials hauling brokers
- Construction gear hauling
- Hauling near me
- Heavy haul rates per mile
- Airplane Shipment
- Oversized tool shipping
- Bulk Freight Conveyance
- Mobile Home Movers
- How Much Does It Cost to Move a Mobile Home?
- Military Freight Services
- Expedited Freight Haulage Assistance
Relevant Statistics
- The global weighty equipment Freight industry is estimated to be worth over $150 billion.
- Approximately 80% of oversized instrument loads are done via sea freight.
- On average, more than 7,500 units are dispatched internationally every month.
- The United States accounts for approximately 30% of the global demand for hefty implements relocating assistance.
- Over 90% of sturdy implements freight involve construction apparatus such as excavators, bulldozers, and cranes.
General Facts
- Heavy shipping involves the forwarding of large and bulky tools or vehicles.
- Specialized trailers and carriers are used to haul safely.
- Due to weight and size restrictions, the cargo process may require permits and coordination with local authorities.
- Freight forwarders and logistics companies often handle dense materials conveyance, ensuring efficient delivery.
- Proper planning, extra time and packing and securing of oversized loads is crucial to prevent damage during the transport process and meet legal requirements.
Resources
Freight Shipping Resource
Construction Equipment Specs & Weight - helpful for construction companies specific requirements when it comes to gross vehicle weight, weight loads, fuel consumption and federal regulations.
If you need to know how much a specific piece of apparatus weighs, that is valuable information for getting a free quote estimate for supplies dispatching.
Frequently Asked Questions
What Is The Average Cost Of Shifting?
The exact price of moving your unit will vary depending on its size and how far you are shipping it.
For example, let’s say that you need to move a piece of equipment on a standard flatbed or flat rack container. The Instruments are being dispatched less than 200 miles. The average cost of getting this unit delivered by the company is approximately $4 to $5 per mile and will take 1 to 3 days to complete.
Now, let’s say that you need to move it 2,000 miles. The rate will likely drop drastically and cost you approximately $2 per mile. However, the estimated time in transit will be about 6 to 9 days from the provider. These are hypotheticals only and not the accurate estimate. Whatever your needs may be, we can quickly provide you with a free quote.
What Type Of Oversized Loads Can Be Moved?
Heavy machinery is a broad term that refers to a wide range of devices used in various industries. This equipment is defined by both its weight and size. Some common examples include:
- Tractors
- Forklifts
- Cranes
- Industrial materials
Machines in this category may require specialty carriers instead of traditional flatbeds. Fortunately, A-1 Auto Transport can facilitate your conveyance needs by connecting you with one of our reputable shippers.
Who Can Provide Insurance Coverage During Hauling?
Licensed dense Implements transporters are required to have cargo and liability insurance in place. to safely move the items. When you schedule your heavy cargo services through us, our policy will protect your apparatus. However, you can purchase supplemental coverage to ensure that your heavy equipment is adequately insured.
If your instruments arrives with unexpected damage, make sure to contact us immediately. We will document the incident and forward the information to our insurance company. They will reach out and walk you through the claims process.
Are There Weight Restrictions?
Yes, the weight of a shipment determines what types of transportation that you will need. Heavy haul shipments cannot exceed 80,000 pounds gross vehicle weight (GVW). If it does, then special equipment and special permits will be required.
The dimensions of your machinery are also extremely important. If your materials are too wide or tall, then the carrier may need to provide pilot and escort vehicles. Making these arrangements takes time, so make sure that you provide detailed information about your equipment’s specifications to the company so that appropriate step deck trailers can be arranged.
What Is The Most Affordable Way To Move?
When it comes to shipping your unit, there are plenty of shipping options available through us. However, open-air shipping is typically the most affordable.
Using this method, your equipment is loaded onto a step deck trailer and left uncovered during transportation. The equipment may be loaded using a flat rack or roll-on/roll-off method, both of which are cost-effective options.
What Is Roll-On/Roll-Off?
Also known as the RoRo method, this option is extremely popular for international transportation. It can also be used for domestic.
As the name implies, this method involves driving the equipment onto flatbed trailers at the pickup location and rolling it off when it arrives at the final destination. RoRo is fast, efficient, and cost-effective.
What Is A Flat Rack Container?
Flat rack containers are great for transporting boats, RVs, and other pieces of equipment. The machinery is secured to a flat rack and is an extremely flexible method used by trucking companies.
Since it is an open-air method, it is also cheaper than using a container. However, your materials will not be protected from the elements once it is loaded from the pickup location. You don't need to acquire permits for this transport.
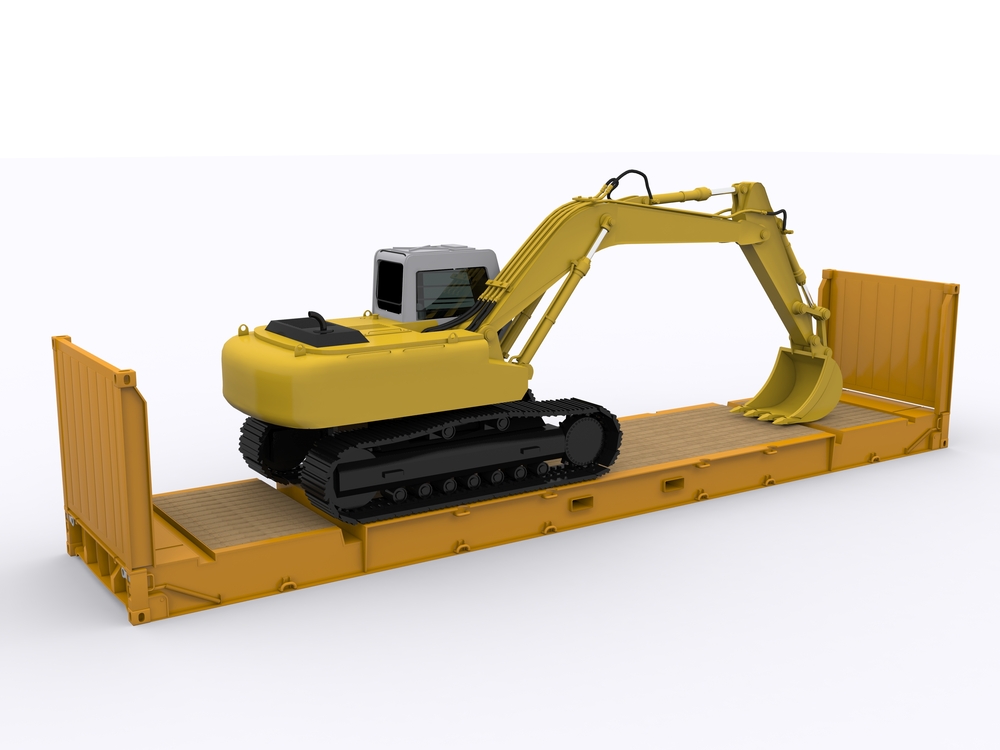
What Is The Lift-On/Lift-Off Method?
The lift-on/lift-off method is best for non-operable vehicles and immobile equipment. This includes engines, farm equipment, and other forms of heavy machinery that cannot be rolled onto a flatbed or ship. When using this method for heavy equipment transport, a large crane will be tasked with loading and unloading your equipment.
When Is A Container Used For Hefty Apparatus Hauling?
Container transport is the safest transportation method. It offers maximum protection against the weather and is great for long-distance transit. However, it is also one of the costliest options available with the shipping company.
Some types of machinery cannot fit in a shipping container. If this is the case for your shipment, you’ll need to find an alternative solution to look for heavy machinery movers near you.
Which Method Should I Choose?
Container is a great choice if your machinery needs added protection. For instance, let’s say that you are moving an industrial boiler. This machinery is not supposed to be exposed to the elements. In this scenario, you should strongly consider container shipping or another covered option.
On the other hand, heavy equipment like front loaders and buckets is extremely durable. This equipment is designed to withstand everything from bad weather to the hazards of being used on a construction site. Open-air would likely offer the best value for such heavy equipment hauling.
Will My Tool Need To Be Disassembled?
Your equipment may need to be disassembled, depending on where your instruments is being shipped to. When transporting equipment internationally, large machines that have a scoop or bucket will need to be disassembled. Some states also prohibit the transportation of weighty materials with buckets attached.
When you’re scheduling your heavy implements services, make sure to ask our team if your equipment needs to be disassembled. We will discuss the requirements of the states on your shipping route.
Can You Help Me To Dispatch My Unit Internationally?
While we specialize in facilitating domestic services, we can also help you find international transit solutions. With that being said, international shipping is much more restrictive. It is vital that you properly prepare your equipment and obtain any required permits.
If you have never shipped heavy instruments internationally before, we can walk you through the process. Our experts have facilitated virtually every type of solution imaginable. The heavy apparatus hauling carriers that we partner with are also extremely experienced with international and will make sure that your equipment safely arrives at its destination.
What Are The Weight Restrictions?
Heavy equipment is limited to 80,000 pounds gross vehicle weight (GVW). If your implements exceeds that limit, then the company will need to obtain special permits.
The carrier may also need to utilize unique hauling equipment like dual-lane trailers, depending on the dimensions of your machinery.
What Is A Cargo Overload?
Overload means that the GVW of your shipment exceeds the vehicle’s capacity. Shipment overload can damage your equipment or the vehicle hauling it. The shipping company may also be fined for shipment overload. These additional fees will often be passed on to you for moving heavy machinery.
Commercial transportation is one of the most strictly regulated industries in the nation. During the course of transit, your carrier will likely have to pass through multiple weigh stations to ensure that they are not overloaded. That is why you must provide the carrier with accurate information when you’re scheduling your heavy equipment transportation.
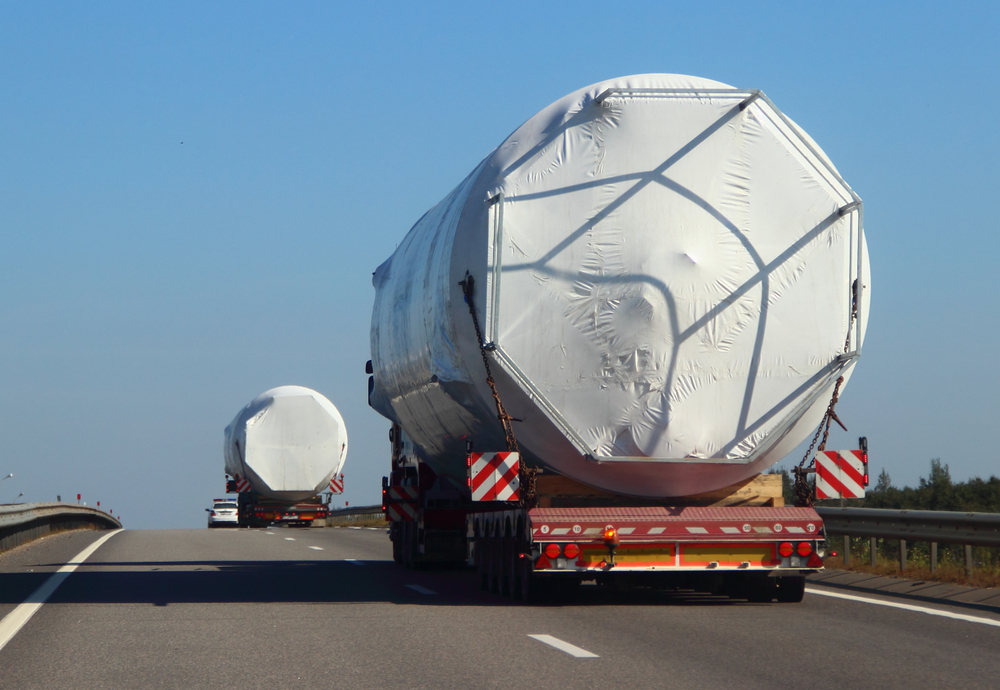
Does All Hefty Apparatus Shifters Near Me Require Permits?
Not all heavy apparatus movers near you requires permits. Some states do require permits, while others do not. International and oversized heavy equipment shipments must have proper permits.
If your heavy implements is “oversized,” the carrier will also need to provide pilot and escort vehicles. These vehicles are usually equipped with lights and banners that warn other drivers that the load is oversized.
It is a good idea to request permits for heavy equipment a few weeks in advance. If you do not have the proper permits when the carrier arrives for pick-up, then they will have to reschedule your shipment.
Do I Need To Pull Permits From Apparatus Movers?
Yes, the equipment owner is required to obtain the proper permits for heavy equipment transport. However, many carriers have staff that can help you navigate this process. If you think that you may need a permit, make sure to discuss this with the A-1 Auto Transport sales team.
Do I Need To Be Present When My Unit Is Being Picked Up?
Yes, you or a representative will have to be present when your heavy equipment is being loaded and unloaded by the heavy materials mover. If someone is not on-site at the scheduled time, then you will need to complete authorization forms in advance.
Without these forms or a representative of your business, the carrier will not be able to load your heavy equipment.
How Long Is My Cite Valid?
A-1 Auto Transport’s quotes are valid until the end of the business day. However, we reserve the right to alter the quote if you require additional services or provide inaccurate information to ship heavy equipment.
We ask that you take the time to collect accurate information about your heavy instruments before requesting a quote. This allows our team to provide more detailed estimates for your heavy equipment transport needs.
While we would like to guarantee quotes longer, factors that impact shipping rates change daily. If you are unable to schedule shipping services by the end of a business day, we will gladly provide you with an updated quote free of charge.
Can I Track The Cargo During Transit?
Most haulers provide real-time satellite tracking for heavy equipment shipments. This means that you can obtain up-to-the-minute information about your machinery. You can access this information from any device that has an internet connection, including laptops, phones, and tablets.
Can I Move Additional Parts With My Load?
Usually, you cannot ship anything but the equipment itself. Small spare parts and other unsecured items pose a safety risk to the driver and other people on the road. However, most carriers can accommodate large items like a second scoop or bucket.
If you need to transport additional pieces of hardware, make sure that you have specific measurements for those items. Convey that information to our sales team and we will do our best to accommodate the request.
Freight carriers will only accept equipment that is on the bill of lading. They cannot transport last-minute add-ons when they arrive at your facility.
Am I Eligible For A Discount?
Many of our carriers offer promotions, seasonal deals, and discounts. These include discounts for:
- Seniors
- Military veterans
- Government employees
- Corporations
Contact our staff to find out if you qualify for any of these great cost-saving opportunities. We can provide you with a free quote and help you to find some ways to save on heavy equipment shipping.
Where Can My Tool Be Hauled?
A-1 Auto Transport works with carriers throughout the nation. We can facilitate local, interstate, and international freight. Just let us know what you need to ship and we will facilitate the shipment process.
When you contact our sales team, let them know where the equipment is being picked up and where it needs to be delivered to. You will receive a free estimate based on the dense apparatus hauling information provided to us.
We will arrange everything and ensure that you find the perfect heavy equipment carrier for your needs.
Can I Choose My Pick-Up Date And Time?
The team makes every effort to schedule heavy equipment shipping services under your requests. However, there are instances in which this is simply not possible. When this happens, we will arrange pick-up as close to your requested date as possible.
Unfortunately, it is a bit more difficult to predict when your instruments will be delivered. Factors such as weather, traffic, and Department of Transportation driving restrictions all come into play. Drivers are unable to travel more than 500 miles in a single day.
With that being said, we provide clients with a projected delivery window. If your heavy equipment shipment experiences drastic delays and will not be delivered within that time frame, we will reach out and notify you. We will maintain open lines of communication until your delivery is complete.
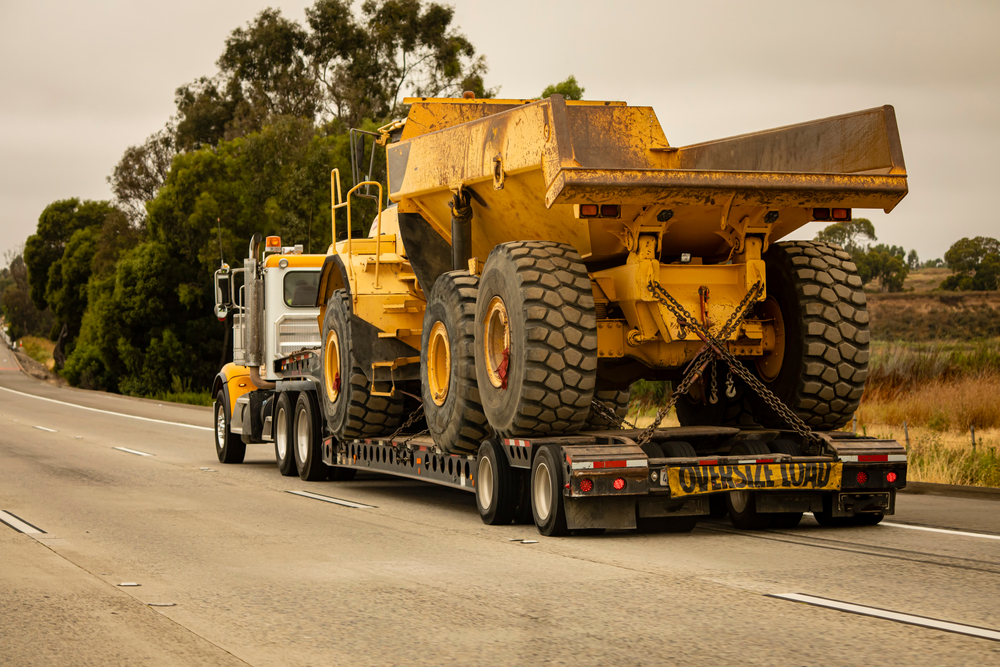
When Should I Book?
We recommend booking your heavy equipment shipping services as early as possible. Clients that schedule pick-ups sooner are more likely to get the date that they request. In addition, shipping rates may be cheaper if you make arrangements early.
The longer you wait, the harder it is to find a carrier that can accommodate your request.
My Load Hasn’t Been Delivered. What Happened?
When you book heavy equipment shipping services with A-1 Auto Transport, we will provide you with a delivery window. Most of the time, equipment arrives within this time frame.
Sometimes, unexpected things happen that can delay your shipment. This may include severe weather, significant traffic issues, or mechanical issues with the transport vehicle.
When delays occur, we will let you know as soon as possible so that you can make any necessary adjustments. You will also be able to track your shipment in real time.
Can I Transit Multiple Pieces Of Gear?
Yes, many clients need to move multiple pieces of heavy equipment at once. We work with top-tier carriers that can handle large shipping requests. You may also be eligible for discounted rates.
However, you must schedule these kinds of bulky materials shipping services early. Loading and transporting multiple pieces of heavy machinery requires planning and coordination. If you wait too long, carriers may charge a premium rate.
Will We Notify Me When My Carrier Is On The Way?
A-1 Auto Transport cannot provide you with an exact arrival time. However, the carrier should contact you 12-24 hours before your scheduled pick-up or delivery date. They will typically give you an arrival window that spans several hours.
If there are any unexpected delays, we will reach out and provide you an update as soon as possible.
What Payment Options Are Available?
At A-1 Auto Transport, we pride ourselves on providing a superior customer service experience. That is why we accept a variety of payment options. Choose the method that is most convenient for you.
My Tool Doesn’t Run. Can It Be Hauled?
Yes, our carriers can move stationary machinery and equipment that is inoperable. There are several loading methods available depending on the size and dimensions of your equipment. This includes crane and forklift loading, just to name a few.
Can You Help Me Transit Tools Bought Online?
Yes, we can coordinate shipping solutions for online heavy equipment purchases. Many of our past clients have purchased heavy machinery via online auctions.
While some auctions provide shipping services, they usually charge premium fees. Partnering with our team is more affordable and efficient. We will get your new machinery delivered to you as quickly as possible.
Is There A Lot Of Paperwork Involved During Pick-Up?
There is very little paperwork involved at the time of pick-up. Usually, you will receive insurance information and a bill of lading. You will also need to provide the carrier with permits (if applicable).
Who Will Be Moving My Gear?
We have partnerships with some of the most reputable heavy equipment haulers in the nation. Our goal is to ensure that your equipment arrives on time and in perfect working order.
At A-1, our core values are transparency, authority, and expertise. We only partner with carriers that share these values.
When you put your trust in A-1, you can expect world-class service and reliable shipping solutions.
How Do You Send Tools?
Sending heavy equipment typically involves specialized transportation services. This can include flatbed trucks, trailers, and even cargo ships for international moves. It's essential to:
- Choose a reputable heavy equipment transportation company.
- Ensure the equipment is properly prepped for transport, which may involve draining fluids, securing loose parts, or even partially disassembling the equipment.
- Work closely with the transport company to understand any permits or documentation required, especially for oversized loads.
What Is The Meaning Of apparatus haulage?
Weighty apparatus carriage refers to the specialized process of moving large and heavy machinery or equipment from one location to another. This can be across short distances, such as within a construction site, or over long distances, spanning cities, states, or even countries. Due to the weight and size of the equipment, this type of transport often requires special vehicles, permits, and expertise.
How Much Does It Cost?
The cost can vary widely based on several factors:
- The size and weight.
- The distance it needs to be transported.
- The mode of transportation (e.g., truck, train, ship).
- Special requirements, such as oversized load permits or escorts.
- The current market rates for shipping services.
It's best to get quotes from multiple transportation companies to get a precise estimate based on your specific needs.
How Do You Dispatch Tool?
Shipping machinery, especially large or specialized equipment, requires a meticulous process to ensure it arrives safely and intact at its destination. Here's a step-by-step guide on how to ship machinery:
Assessment and Preparation: Begin by taking detailed measurements and understanding the weight of the machinery. This will help in determining the best transportation method and potential costs. Depending on the type of machinery, certain parts might need to be secured, removed, or protected.
Cleaning: Before transportation, machinery should be cleaned to remove any dirt, grease, or residue. This is especially important for international shipments, where customs regulations might require machinery to be free of soil and contaminants.
Documentation: Prepare all the necessary documents. This could include manuals, shipping manifests, customs documentation (if shipping internationally), and any required permits or certifications.
Select a Reliable Transportation Company: Due to the complexities involved in transmitting machinery, it's crucial to choose a transporter with experience in machinery shipments. They should have the appropriate equipment and know-how to handle your machinery's specific needs.
Determine the Shipping Mode: Depending on the machinery's size, weight, and destination, various transport modes could be used, including:
- Flatbed trucks or specialized trailers for over-the-road transportation.
- Freight trains for long-distance domestic shipping.
- Cargo ships or airplanes for international shipments.
- Loading and Securing: Use equipment such as cranes or forklifts to load the machinery. Once loaded, the machinery should be securely fastened using straps, chains, or other securing methods to prevent movement during transit.
Insure the Shipment: Given the value of machinery, it's crucial to have appropriate insurance coverage. Ensure that the transporter's insurance covers potential damages, and consider purchasing additional coverage if needed.
Monitor the Shipment: Many transport companies offer tracking services, allowing you to keep an eye on the progress of your machinery. It's also a good practice to maintain communication with the transporter, especially during longer shipments.
Customs and Duties (For International Shipments): When shipping internationally, you'll need to be aware of customs regulations, potential tariffs, and import/export duties. Ensure all paperwork is in order and anticipate potential inspections or delays at customs checkpoints.
Unloading and Installation: Once the machinery arrives at its destination, similar equipment used for loading (like cranes or forklifts) will be required for unloading. After unloading, inspect the machinery for any damage. If the machinery requires assembly or installation, ensure that you have the necessary tools and expertise on hand.
Post-Shipment Review: After the machinery is successfully shipped and installed, review the shipping process. This can help identify any areas for improvement for future shipments and solidify relationships with transporters who provide excellent service.
Feedback and Review: After the shipment, take a moment to provide feedback to the transportation company. This can be beneficial for both parties involved. Your feedback can help the company improve its services, and a positive review can bolster its reputation.
Documentation Archiving: Ensure that all paperwork related to the shipment – from contracts to customs documentation – is properly archived. This is important not only for tax or business record purposes but also in the event of any disputes or claims that may arise later.
Maintenance Check: After shipment, especially for long distances or international destinations, it's a good practice to do a thorough check of the machinery. Ensure that it's still in good working order, and address any minor issues that might have arisen due to the shipment process.
Build Relationships: If your business frequently ships machinery, building a strong relationship with reliable transport companies can be beneficial. Over time, they might offer you preferential rates, better slots, or even priority services due to the established trust and volume of business.
Stay Updated with Regulations: If you're frequently shipping machinery, especially internationally, it's crucial to stay updated with changing customs regulations, import/export duties, and transportation laws. This proactive approach can help avoid potential hiccups in future shipments.
Safety First: Always prioritize safety, both for the machinery and the people handling it. Ensure that all personnel involved in the loading, transportation, and unloading processes are adequately trained and equipped with the necessary safety gear.
Contingency Planning: While careful planning can prevent many issues, it's always wise to have contingency plans in place. This could be in the form of backup transporters, additional insurance, or plans for machinery repairs in the event of unexpected damages.
Budgeting and Cost Analysis: After shipment, compare the actual costs with initial estimates. This will help in budgeting for future shipments and might reveal areas where savings can be made.
Continuous Improvement: As with any business process, always look for ways to refine and improve your machinery shipping procedures. Whether it's finding more cost-effective transport solutions, streamlining the preparation process, or negotiating better terms with transporters, there's always room for enhancement.
By following a comprehensive approach to machinery shipping and continuously refining the process based on experiences, businesses can ensure that their valuable equipment is transported safely, efficiently, and cost-effectively.