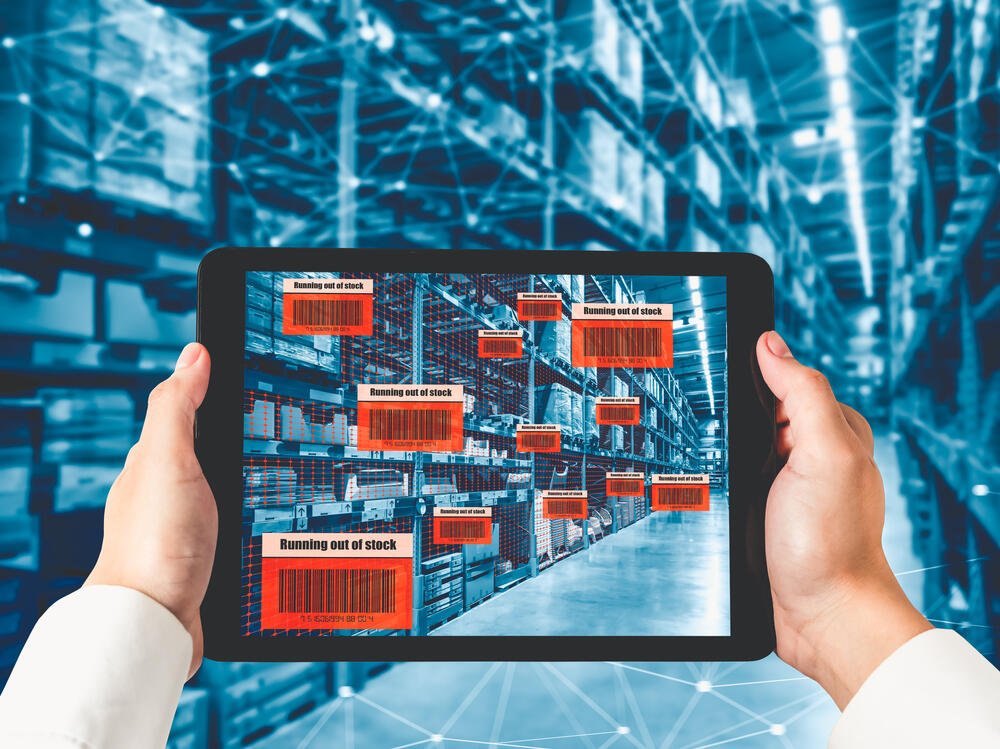
Supply chains are complex networks of companies, products, and services that move from supplier to customer. They are vital to our economy because they enable businesses to efficiently deliver goods and services to customers.
But supply chains also pose a significant risk to businesses. In order to manage these risks effectively, businesses must understand how they work and identify where potential problems may occur. Understanding the supply chain's structure and identifying and managing its risks are necessary for accomplishing this.
In this blog, we will look at the basic concepts behind supply chains and how they operate. We will also examine the most common types of risks associated with supply chains and how to mitigate them.
Identification, evaluation, and mitigation of hazards throughout your whole supply chain are all part of supply chain risk management. This includes risks related to products, people, processes, technology, and information.
Internal risks include those that occur inside your organization, while external risks come from outside parties. Both types of risks must be identified and managed properly to ensure an uninterrupted flow of goods and services.
What Are Some Supply Chain Risks?
As we mentioned earlier, there are many different types of supply chain risks that can impact businesses. These risks can originate within your organization — such as internal supply chain management — or from external sources. In fact, some of the most common supply chain risks are actually caused by things happening outside of your control. For example, the following supply chain risks are caused by events occurring outside of your control:
Demand risk
This occurs when you miscalculate the amount of product that needs to be produced each month. An effective illustration of this is when a client cancels a sizable contract. Another example is when a competitor offers better pricing.
Delivery risk
This happens when the raw resources your company needs aren't delivered on schedule or at all, disrupting the flow of goods, components, and supplies.
Ecological risk
Social-economic, political, governmental, or environmental problems that have an impact on the timeliness of any part of the supply chain directly cause environmental risk in the chain.

The risk from the environment
Social-economic, political, governmental, or environmental problems that have an impact on the timing of any aspect directly cause environmental risk in the supply chain.
Political risk
The possibility that governments could change their laws or policies is known as political risk. This can make it more difficult for vendors to supply your company with goods or services.
Labor risk
Labor risk is the possibility that your employees will not show up for work or will be unreliable.
Technology Risk
Technology risk is the chance that your company's current systems won't
Legal Risk
Legal risks in the supply chain are the direct result of uncertainty regarding legal and regulatory requirements that affect the timing such as product delivery.
Currency risks
Risks that do not come from within your organization but instead arise from external factors that affect your costs and income.
Information Risk
Information risks in the supply chain stemming from the loss of data or other forms of information that could cause delays or interruptions in the flow of products,
Internal and external Supply Chain Risks
Supply chain risk assessment software is now widely used across industries to identify and monitor potential risks throughout the entire supply chain. These tools can assist companies in anticipating issues and making the necessary plans.
However, there are many different types of supply chain risks, including manufacturing, business, planning and control, and logistics, among others.
While internal supply chain risks are often easier to manage than external ones, they are nonetheless unavoidable. They include things like missing deadlines, poor quality products, unplanned inventory levels, overproduction, and missed shipments.
Supply chain risk management strategies fall into two categories: mitigation and prevention. Mitigation involves taking action to prevent disruption from occurring. Prevention means identifying and managing risks as soon as possible.
Strategies for Supply Chain Risk Management
The two types of supply chain risk management solutions are prevention and mitigation. Mitigation involves taking action to prevent disruption from occurring. Prevention means identifying and managing risks as soon as possible.
Monitor your risk levels
There are several online resources that provide information about specific types of supply chain risks. For example, here are five articles discussing how to prepare for a natural disaster
Make sure you have good data
The best way to avoid supply chain risks is to have accurate data. If you don’t know what you need to produce, it’s impossible to make informed decisions.
Be prepared
If you want to minimize the impact of supply chain risks, you must be prepared to respond quickly. The likelihood of disruptions decreases with your level of preparation.
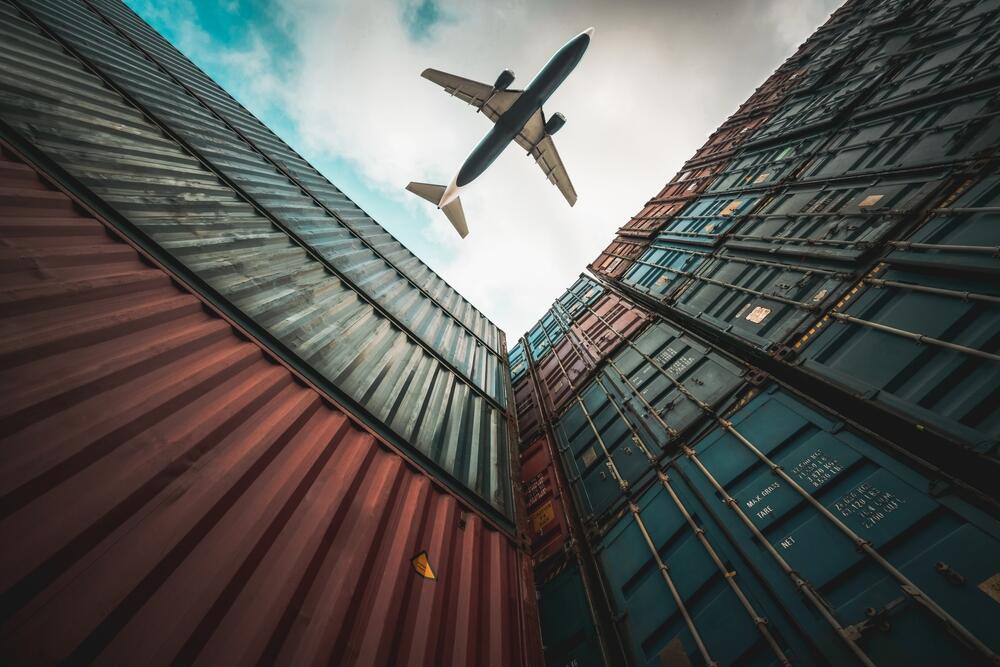
Plan ahead
Planning ahead will allow you to determine whether you have adequate capacity to meet demand. You'll be able to alter as needed thanks to this.
Build in flexibility
When planning for a major event, such as a hurricane or earthquake, you should build flexibility into your plans. This will guarantee that you can adjust to shifting circumstances.
Track inventory
Keeping track of inventory levels will help you predict future demands. This will give you time to adjust production schedules and purchase additional supplies.
Establish emergency plans
Establishing emergency plans will help you respond quickly to unexpected events. These plans should include procedures for contacting suppliers, employees, and customers.
Establish supplier relations
Building trusting connections with your major suppliers is crucial. By doing this, you'll be better able to spot problems before they develop into larger ones. Check Up On Your Vendors By keeping an eye on your vendors, you can spot any issues early on. You will then have the chance to resolve them before they have an impact on your company.
Monitor your vendors
Monitoring your vendors will help you identify any problems before they escalate. This will give you the opportunity to address them before they affect your business.
Maintain quality control
Maintaining quality control ensures that products meet customer expectations. This will help you maintain brand loyalty and reputation.
Ensure compliance
Ensuring compliance is essential to maintaining legal requirements. This includes ensuring that workers are paid properly and that product safety standards are met.
Use technology
Technology can help you manage supply chains more efficiently. The software can be used, for instance, to track inventory and track shipments. Online technologies can be used to communicate with suppliers and clients.
Be vigilant
Be vigilant about potential threats. If something seems amiss, contact authorities immediately.
Keep records
Keep records of past disruptions and incidents. You will have a better understanding of past events and how they might occur in the future as a result.
Improve communication
Improve communication among all parties involved. You can avoid misconceptions and misunderstandings by doing this.
Form a team to incidents response team
In order to handle emergencies, establish an incident response team. You'll be able to respond quickly and effectively as a result.
Have a crisis management plan
Develop a crisis management plan to deal with situations that threaten your company. This will help you minimize damage and restore operations as soon as possible.
Document processes
Document processes to make sure they're followed consistently. This will help you prevent errors from occurring.
Train employees
Train employees on their roles and responsibilities. This will help them perform their jobs correctly.
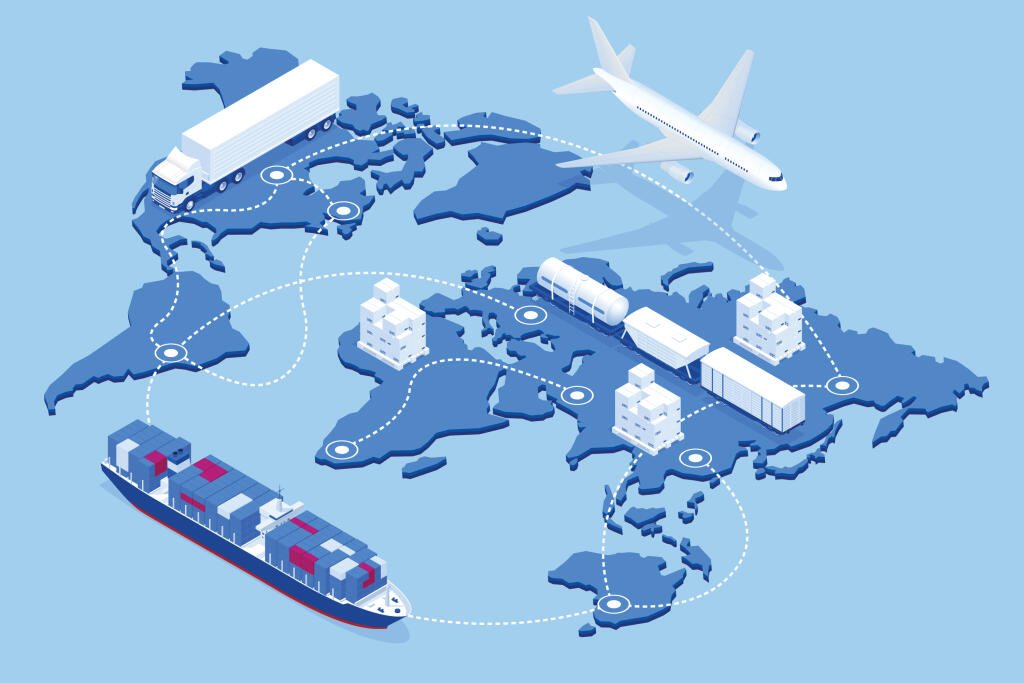
Five Techniques to Manage Supply Chain Risk
Managing your supply chain risks is no easy task, here are some techniques to help you along the way
Technique 1:
Innovation and efficiency in contracting management
Innovation and efficiency in contracting management refer to the process of identifying and selecting appropriate contracts. It involves evaluating contract terms and conditions to determine whether they are suitable for your organization.
When selecting a contract, the following elements must be taken into account:
- The type of contract (fixed-price vs. cost plus)
- The duration of the agreement
- Payment terms(e.g., lump sum or periodic payments)
- Contractor performance evaluation criteria
- Contractor performance history
- Contractor financial stability
- Contractor insurance coverage
- Contractor bonding
- Contractor indemnification
- Contractor liability insurance
- Contractor dispute resolution mechanism
- Contractor dispute settlement mechanism
- Contractor security clearance
Technique 2:
Strategic requirements for supplier insurance and limitations of liability
Strategic requirements for supplier insurance and limits of liability refer to the procedures used by companies to protect themselves against losses due to third-party claims.
Supplier insurance protects companies against loss resulting from the acts or omissions of their suppliers. Limitations of the liability limit the number of damages that a company may recover if it loses a claim.
Supplier insurance coverage
- Provides protection against legal actions brought by third parties who have suffered economic loss because of the act or omission of the insured.
- Protects the insured against direct physical loss or damage caused by the insured's own negligence or will full misconduct.
Limitations of liability
- Limits the number of damages that the insured may recover in any action arising out of the insured's failure to meet contractual obligations.
- Limits the number of damages the insured may recover in an action based upon strict tort liability.
- Limits the total amount of damages that the insurer may pay under all policies issued to the insured.
- Limits the maximum dollar amount of damages that the company can collect from one person or entity.
- Limits the number of persons or entities entitled to receive a recovery.
Technique 3:
Provider optimization and redundancy
Provider optimization and redundancy refer to the process of determining which providers can provide services at the lowest cost while maintaining quality standards.
The concept of having many sources of supply for essential commodities is known as redundancy.
For example, if one source goes out of business, another source can take over. Redundancy aids in maintaining service continuity. Utilizing resources effectively is the practice of optimization.
Utilizing resources effectively is the practice of optimization. For example, if you need to purchase a large quantity of a product, purchasing it from the cheapest provider may not always be the best option. You should consider other factors such as availability, delivery time, and price.
Finding the best method to distribute goods and services when outsourcing is crucial. This includes considering the following issues:
- Availability of materials and equipment
- Delivery times
- Cost of transportation
- Quality of products
- Timely delivery
- Customer satisfaction
- Productivity
- Labor costs
- Training costs
- Maintenance costs
- Repairs
- Overhead expenses
- Capital investment
- Insurance costs
- Taxes
- Legal fees
- Other overhead costs
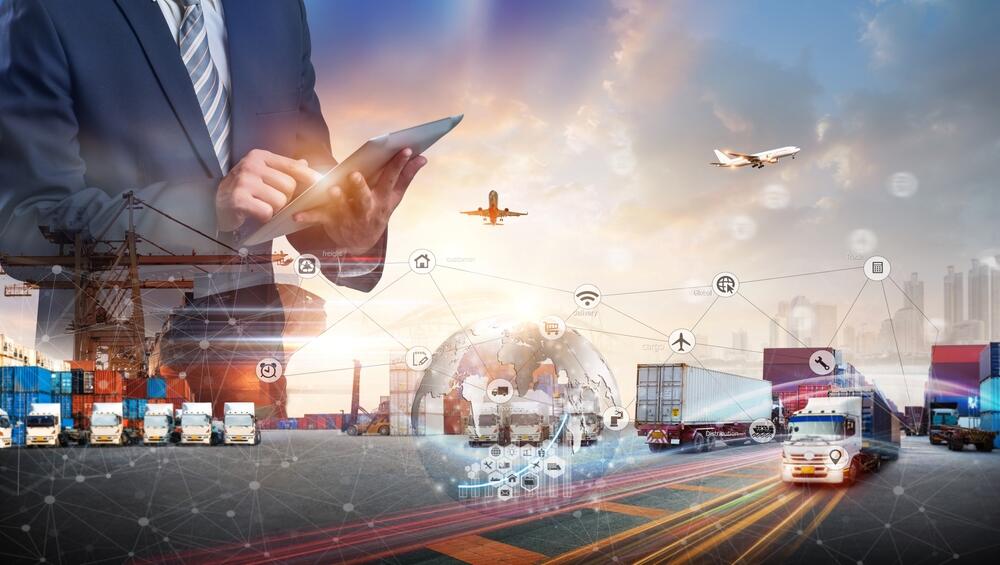
Technique 4:
Supplier financial stability visibility
Supplier financial stability visibility refers to the ability of a company to monitor the financial health of its suppliers.
Financial stability includes:
- Cash flow
- Accounts receivable
- Inventory levels
- Sales Volume
- Customer complaints
- Product returns
- Quality problems
- Labor issues
- Legal actions
- Litigation
Technique 5:
Proper diligence in operational supplier assessment reviews
Proper diligence in operational supplier assessment reviews refers to the process of assessing potential risks associated with a supplier's operations.
Operational risk assessment reviews involve examining the following areas:
- Operational processes
- Personnel qualifications
- Training programs
- Equipment maintenance
- Facilities
- Safety practices
- Compliance with laws and regulations
- Environmentally friendly behavior
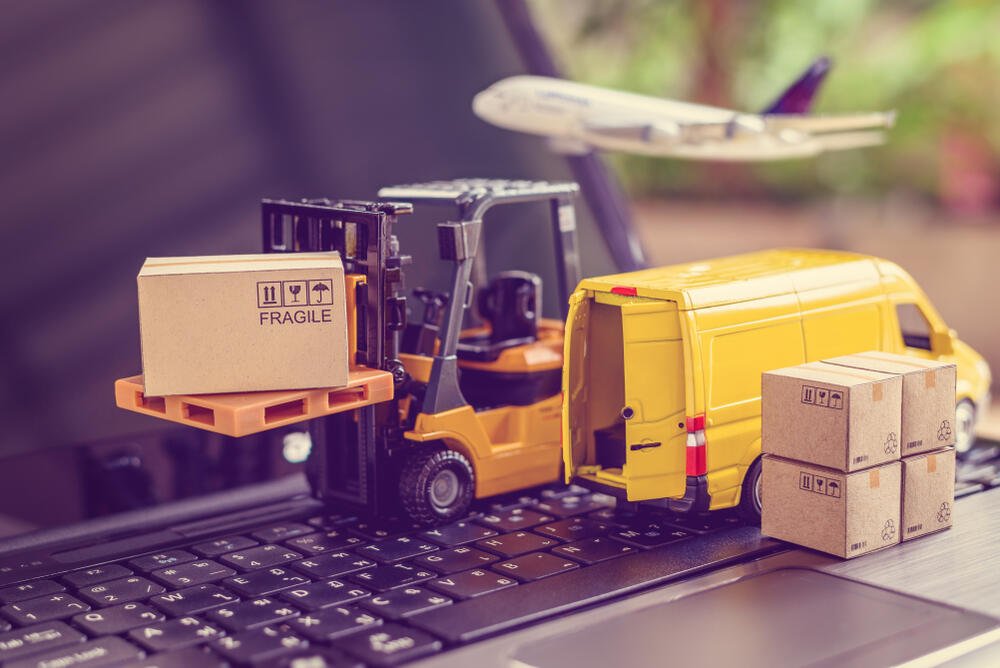
Conclusion
The management of supply chain risk is an essential part of any business's overall strategy. By identifying risks early, companies can take steps to mitigate their impact before they become problems. This will save money and resources down the line. For more valuable information check out our content-packed blog. You'll be surprised at how many answers you'll get, all in one place.
At A-1 Auto Transport, we offer comprehensive shipping services to meet the needs of your business. As one of the premier shipping companies in North America, we have years of experience shipping both domestically and internationally.
Contact us today to inquire about our heavy equipment shipping services. We look forward to hearing from you!