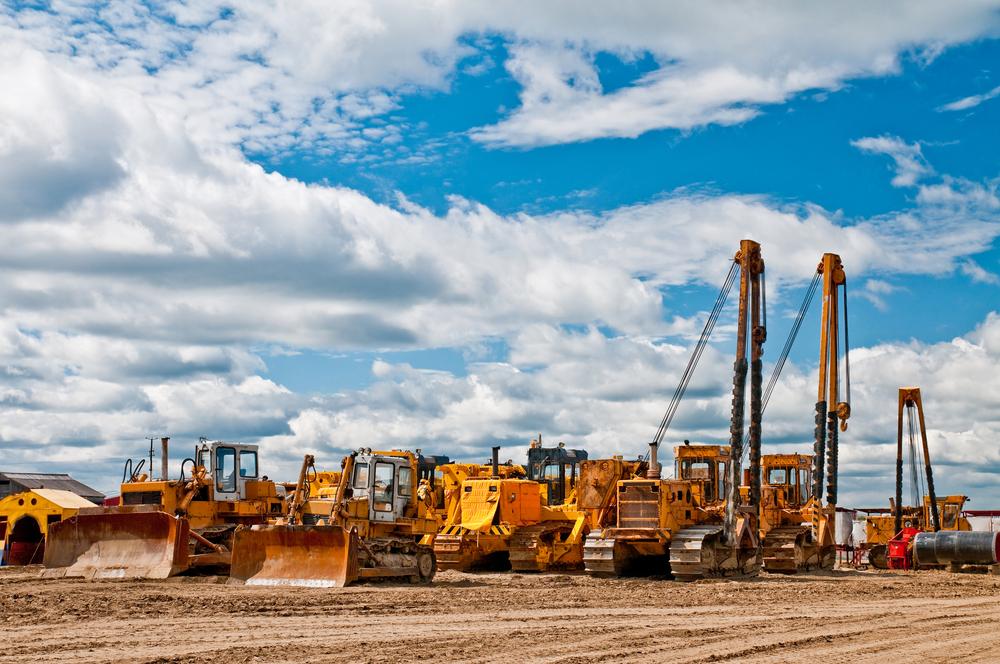
Heavy machinery is vital in many industries, such as construction, mining, forestry, and energy. Whether lifting heavy loads, digging trenches, or clearing land, this powerful equipment helps drive productivity and economic growth.
However, heavy machinery can pose severe risks to safety, the environment, and a company's bottom line if not adequately secured. With construction projects rising globally and equipment becoming more advanced, it is increasingly essential for companies to implement robust security systems for their heavy machinery fleets.
This article provides an in-depth look at the risks of unsecured heavy machinery, discusses best practices for securing it, compares different security system options, and offers guidance on implementation with real-world case studies.
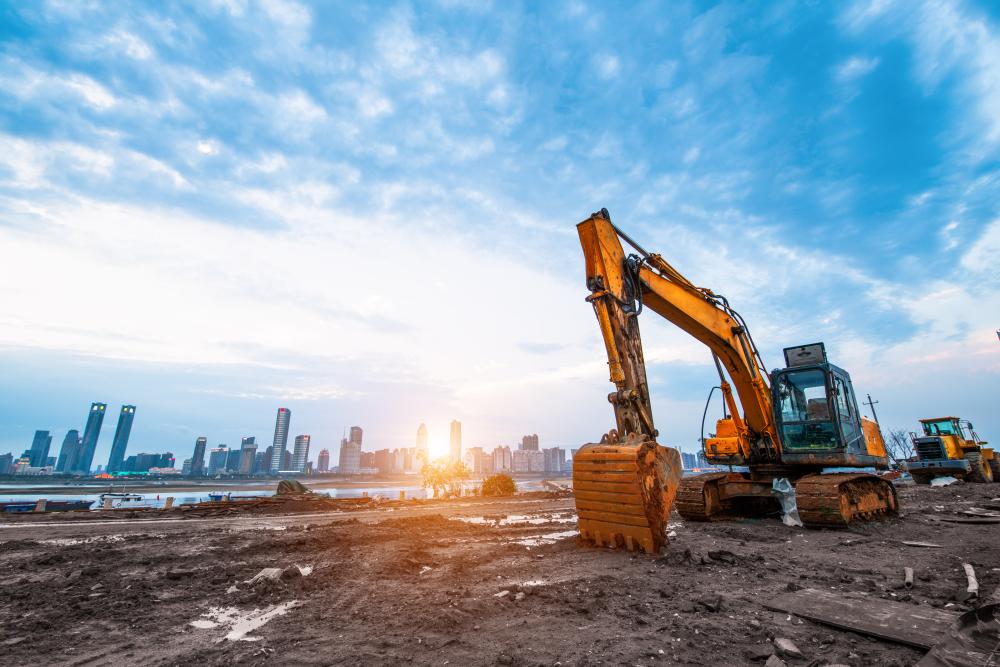
Understanding Heavy Machinery
To properly secure heavy machinery, one must first understand what types of equipment are being protected. In general, heavy machinery refers to compelling vehicles and equipment that are large and perform tasks that require significant physical effort by humans.
Examples include bulldozers, excavators, loaders, cranes, graders, scrapers, forklifts, dump trucks, and more.
Heavy machinery can be broadly classified into various categories based on their functions. Earthmoving machinery such as excavators, loaders, and backhoes dig, lift, and move soil, sand, rubble, and other materials.
Material handling equipment like cranes, forklifts, and heavy-duty trucks are used to lift and transport heavy loads over short or long distances. Road construction machinery, including graders, compactors, and pavers, are used to level, compact, and pave surfaces.
Each type of heavy machinery consists of a power source, chassis/undercarriage, work attachments or lifting mechanisms, and hydraulic or electrical systems to control movements. Proper operation requires training on different heavy equipment types' unique components and functions.
Risks Associated with Heavy Machinery
Unsecured heavy machinery poses risks to safety, the environment, and operational costs. Accidents can cause injuries, fatalities, equipment damage, project delays, and legal/financial liability. Some key risks include:
- Theft of Machinery - With resale values of hundreds of thousands of dollars, heavy equipment is a target for thieves. Stolen machinery ends up supporting illegal activities and costs owners large insurance claims.
- Vandalism and Unauthorized Use - Left unattended, idle machinery risks vandalism through graffiti or property damage. Criminals may also operate equipment without proper training, leading to accidents.
- Environmental Damage - Machinery moving offsite can cause soil erosion, water/air pollution from spills, destruction of vegetation, and harm to wildlife if not appropriately contained.
- Worksite Accidents - Workers on foot or in other equipment are at risk if machinery unexpectedly starts moving due to theft or control system tampering. Falling/tipping loads also threaten adjacent worksites.
- Project delays - Equipment damage or loss results in delays that increase labor costs and penalties for missed deadlines. Downtime also reduces productivity and bid competitiveness.
- Legal Liability - Owners may be legally and financially liable for accidents, injuries, or environmental damage caused by stolen or misused heavy machinery.
Securing heavy machinery can help avoid risks that negatively impact safety, budgets, reputations, and project timelines or quality. Other measures like signs, barriers, and surveillance also aid security efforts.
Securing Heavy Machinery
Heavy equipment owners and operators need to implement comprehensive security measures given the potential hazards. Key factors to consider when securing machinery include:
- Immobilization - Devices like ignition interlock controls and brake locks can stop thieves from moving or operating equipment without authorization.
- Access Restriction - Cab locks, doors, and sealed/locked compartments restrict access to critical components inside or underneath machinery.
- Visibility - Obvious signage warns against trespassing, while surveillance cameras help monitor remote worksites.
- Enclosure - Machinery can be stored in gated and fenced yards with alarm systems when not in use. Containing it prevents thieves from even reaching targets.
- Software Tracking - Electronics and software that monitor location, unauthorized movements, and geofencing provide transparent tracking to catch thieves.
- Operator Authentication - Biometric or keypad systems only allow trusted operators to start machinery through fingerprint/face/password verification.
Proper security requires assessing risks and implementing Layered protections combining physical and technological solutions. Regular reviews ensure security keeps pace with evolving threats.
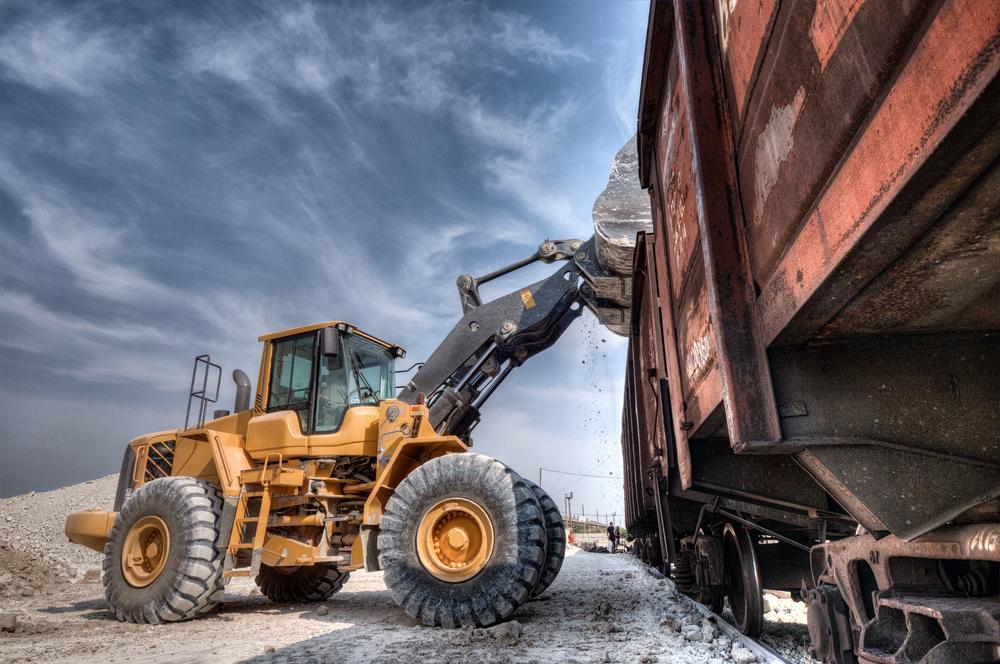
Types of Heavy Machinery Security Systems
Several system options exist to secure heavy equipment depending on a company's budget, fleet size, and security priorities. Integrated solutions deliver the most robust protection.
Tracking Systems real-time
Tracking systems use GPS, network access, and web-based software to monitor locations and report abnormal activity in real time. Devices are securely mounted inside cabs and operate on private networks/satellites. Tracking aids recoveries and provides forensic data for investigations/insurance claims.
Access Control Systems
Access Control uses physical or electronic locks, ignition kill switches, and keypads/biometrics for two-factor authentication. Only validated operators can start machinery through integrated dashboard controls. Solutions range from essential door/cab locks to advanced authentication and immobilizers.
Alarm Systems
Alarm systems detect unauthorized access or activity and notify security or owners through sirens, texts, calls, or web alerts. Basic motion or door sensors trigger bright strobes or sounds, while integrated systems activate video recording and GPS tracking for remote incident response.
Video Surveillance
Networked security cameras record worksites and storage yards to monitor for intruders and review past incidents. Surveillance aids investigations, acts as a deterrent, and allows remote incident monitoring for faster security responses.
Combination Systems
Most advanced integrated systems marry tracking, access controls, and alarms with centralized remote monitoring for 24/7 layered protection. Machinery receives end-to-end coverage through a single-vendor managed solution based on each client's unique risks.
While more complex systems require higher investments, insurers often provide discounted premiums that offset total costs over the years. Fleet size, risk factors, and budget ultimately determine the optimal security approach. Integrated systems deliver the most robust ROI through comprehensive protection and operational efficiencies.
Implementing Heavy Machinery Security Systems
Proper implementation involves assessing security requirements, selecting and installing appropriate systems, and thorough training and maintenance planning.
Auditing machine risk levels, existing protections, and site characteristics help understand fundamental security gaps. Installers then survey areas and propose tailored solutions considering locations, equipment types/values, and usage schedules.
Installation includes securely mounting all system hardware, programming customized operating parameters, and integrating different components via wired or wireless networks established during controlled site outages.
Training educates administrators, operators, and maintenance teams on new system operation, bypasses/overrides for emergencies, routine status checks, and incident response procedures. Periodic refreshers reinforce safe usage.
System integration tests verify all functions—tracking, access controls, alarms, etc.—work seamlessly together as designed. Adjustments address any gaps found before launch.
Maintenance planning schedules software/firmware updates, battery replacements, perimeter checks, and repair timelines to uphold continuous protection reliability over equipment lifecycles.
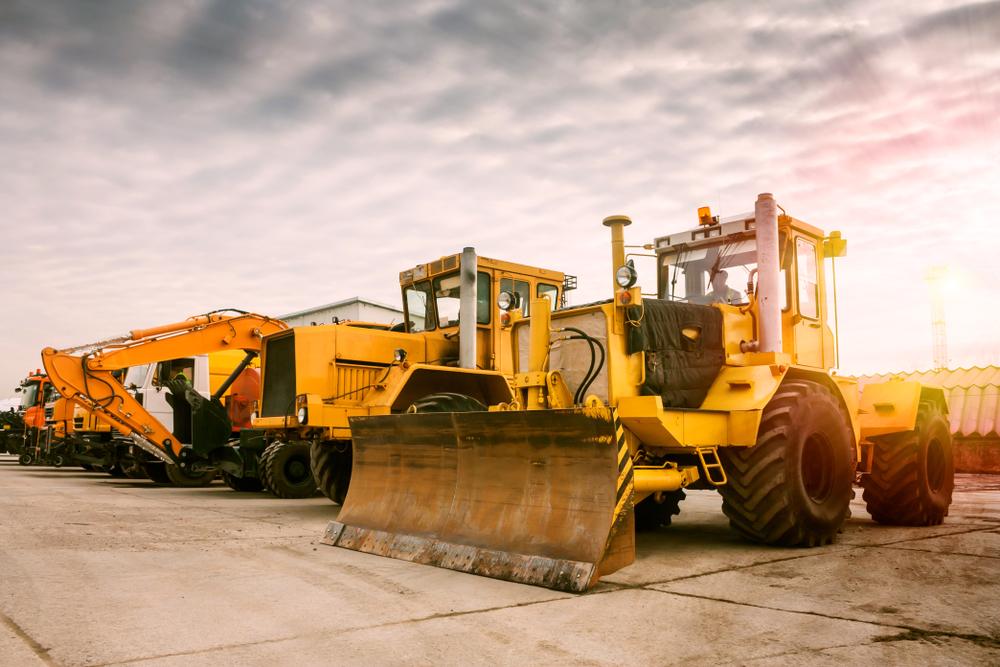
Final Thoughts
As advanced as heavy machinery has become, it remains vulnerable without physical, solid, and technological security measures. Owners and operators must implement layered protections for equipment, workers, and the communities and environments they impact. Forward-looking companies recognize quality security as enabling higher productivity more safely over the long-run.
With risks continuously evolving, industries must keep security capabilities ahead of threats through iterative improvements informed by data analytics and new technologies. The case for robust, integrated heavy machinery security systems will grow more compelling in the years ahead.
Heavy machinery requires robust security due to the high risks and costs of theft, damage, or environmental incidents. Let A1 Auto Transport safely transport your heavy equipment fleet nationwide.
Get a free quote.